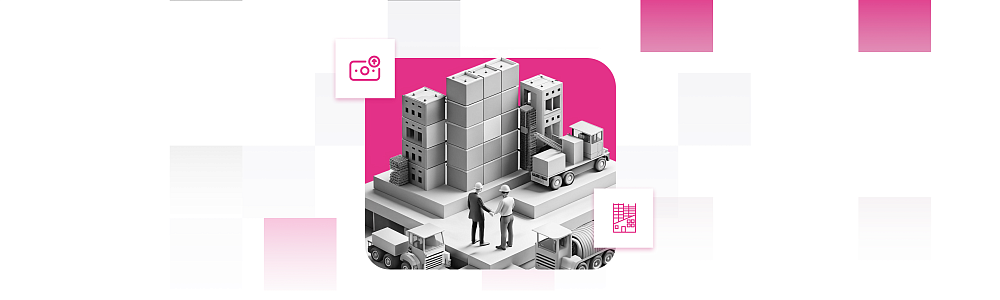
Incentives That Can Boost Investment in Off-site Construction
Other benefits include designs that better fit resident's needs, higher construction quality, and strict adherence to design plans due to the more controlled environment. Modular construction can also be more sustainable, It creates less mess and pollution, uses materials more wisely, and often includes more recyclable options.
New designs adoption will shift profit pools, benefiting some industry players more than others. For example, real estate developers could see higher margins due to better executed projects, but they could also see pricing pressure as risk levels drop.
Challenges the Construction Industry Faces
Another significant challenge in the industry is its divided nature. The different roles for investors, architects, manufacturers, and construction firms, has made it difficult to adopt new design methods.
Architects and designers usually focus on how things work and look, but not on how to make them. They need to collaborate with manufacturers to better understand production. Encouraging more companies to adopt IDC requires these professionals to unite and jointly handle expenses. According to the report, this cooperation could result in better profits in the future.
The industry also faces other inefficiencies such as custom project needs, changing economic conditions, varying interest rates, and the uncertainty of long-term projects. A scattered network of smaller players and varied building regulations in different places discourage progress and hurt productivity. Meanwhile, ongoing issues among main parties delay the shift to off-site construction.
Adoption of the IDC: Collaboration is Key
of your processes and scale your business with FirstBit ERP now!