A staggering 20% of project costs are often attributed to inefficiencies tied to asset handling [?]— whether it’s delays caused by unavailable equipment, maintenance issues, or improper tracking of materials. If you’ve found yourself battling cost overruns, missed deadlines, or unexpected downtime, you’re not alone.
The truth is, construction asset management isn’t just about having equipment and materials on hand; it’s about knowing where they are, how they’re being used, and ensuring they’re maintained properly so that the entire project runs smoothly. From tools and machinery to vehicles and materials, every asset plays a crucial role in delivering your project on time and within budget. If any of these elements are underutilized, misplaced, or inadequately maintained, you’ll quickly face unnecessary delays and increased costs.
This guide is here to help you cut through the complexity. We’ll break down the core principles of effective construction asset management and provide you with strategies to better track and maintain assets. The goal is to help you maximize the lifespan and utility of your assets, prevent costly mistakes, and ensure every part of your project is operating efficiently.
What is a Construction Asset?
Every construction company owns valuable assets. These might include equipment like excavators and cranes or the expertise of skilled workers. When needed, these assets can be turned into money, either by selling them or using them to earn income.
Think of a construction company without its equipment or skilled workers—it couldn't function. That's why these assets are so crucial for success. But managing lots of heavy machinery and coordinating skilled workers isn't easy. It's like trying to conduct an orchestra where each instrument is both valuable and complex.
4 Types of Construction Assets
In construction, assets come in several important forms.
- Fixed assets are your long-term investments – the big-ticket items like cranes, bulldozers, and buildings that you'll use across many projects. These are the workhorses of your operation. They are expensive to buy but vital for getting work done year after year.
- Current assets are the everyday materials that keep your projects moving forward. Unlike fixed assets, these are items you'll use up as you work – things like nails, lumber, cement, and small tools. They're constantly being purchased and replaced as you complete projects.
- Then there are intangible assets, which you can't physically touch but are just as valuable to your business. These include your building permits, project designs, and software licenses. While they might just seem like paperwork, they're essential for your company's ability to operate and compete.
- Finally, there's your most valuable asset: human assets. This includes skilled artisans and engineers, project managers, and construction workers. Their knowledge, experience, and skills truly bring your projects to life. While other assets can be replaced, your team's expertise is what sets your company apart.
Why is Managing Construction Assets Important?
The success of your construction projects hinges on how well you manage your equipment and tools. When excavators sit idle, tools go missing, or machinery breaks down unexpectedly, both timelines and budgets suffer.
Managing construction assets is like having a smart system that helps you:
-
Buy the right assets at the right time
-
Keep track of where everything is
-
Make sure equipment is well-maintained
-
Use resources efficiently
-
Get the most value from your investment
Construction projects are complex challenges where every minute and dirham counts. Without proper asset management, projects can quickly spiral out of control — a reality that many construction companies face daily in the UAE.
According to a recent McKinsey report, large construction projects typically take 20% longer to finish than scheduled. They are up to 80% over budget, often due to poor asset management and resource allocation.[?]
Unexpected equipment breakdowns create a serious financial problem. When a machine stops working, you're not only paying for repairs - you're losing money every hour your project stands still.
Having a good system to manage your equipment helps avoid these problems. Regular checks and maintenance prevent sudden breakdowns, and proper tracking ensures you have the right machines ready when your team needs them.
We also need to consider safety, which is a top priority in UAE construction. The UAE Ministry of Labour reports that many accidents on construction sites involve equipment problems. By keeping machines well-maintained, we protect both workers and projects.
5 Key Steps of Construction Asset Management
With millions tied up in equipment and tools, construction companies can't afford to guess where their assets are or when they need maintenance. A five-step approach turns this potential chaos into measurable efficiency.
1. Planning
Begin with thoroughly assessing your equipment needs based on project scope and timelines. For example, on a 12-month commercial project, you'd assess that you need excavators for site preparation (3 months) and tower cranes for the full duration. That's how you plan that the excavators can be rented short-term, while purchasing the frequently-used power tools would be more cost-effective.
Engage project managers and site supervisors throughout the process to capture real operational requirements and anticipate potential challenges before they impact your workflow.
2. Procurement
Start your procurement process by vetting multiple suppliers against your equipment specifications and budget requirements. When vetting suppliers, look beyond price quotes. Compare equipment specifications, maintenance records, and service reliability. For instance, a supplier offering 24-hour repair service and extensive parts inventory might be worth the higher cost versus one with lower prices but limited support.
Once vendors are selected, establish standardized purchasing procedures that include detailed documentation of costs, delivery schedules, and warranty terms. For instance, create a standard checklist for every equipment purchase: document the base price, delivery fees, and maintenance package costs in a centralized spreadsheet. When ordering a new forklift, your procedure should capture key details like the $45,000 purchase price, scheduled delivery date, 3-year/3,000-hour warranty terms, and included maintenance visits.
Track vendor performance through a structured evaluation system, ensuring all stakeholders have clear visibility into purchase approvals and delivery timelines. For example, the ERP system automatically tracks each vendor's delivery times, pricing changes, and service quality. When XYZ Rentals' prices increase by 15% or their response times exceed 48 hours, the system flags these changes for review and comparison with other vendors.
3. Monitoring
Deploy a digital tracking system that monitors equipment location and usage in real-time, supported by regular physical inventories to verify asset conditions. Build performance dashboards showing critical metrics like using rates and maintenance status, then use this data to optimize equipment allocation across sites and identify trends through monthly performance reports.
For example, FirstBit ERP software for construction includes real-time tracking tools and a mobile app where operators can log equipment hours and conditions. Using these features, you can see that Excavator #103 has been used for 45 hours this week at Site A, needs scheduled maintenance in 20 hours, and its current location is at the correct job site.
The system's dashboard displays this data alongside usage charts, helping you spot patterns like certain equipment sitting idle 40% of the time or specific sites consistently overusing their allocated machinery.
4. Maintenance
Create a maintenance schedule based on manufacturer specs and real-world usage, then train your team to follow step-by-step inspection checklists using digital tools or mobile apps. Back this up with a streamlined parts inventory system that tracks stock levels and automatically triggers reorders while keeping detailed digital logs of all repairs and costs to spot recurring issues quickly.
For example, set up simple daily checks in your maintenance app: operators mark off items like 'Check oil level' and 'Inspect tracks' before starting work. When oil levels are low, they snap a photo and the system automatically alerts maintenance. If the same $200 hydraulic hose keeps breaking every month, your repair log quickly shows this pattern versus spreading repairs across multiple machines.
5. Disposal
Monitor equipment performance metrics through maintenance software to flag machines that show declining efficiency or rising repair costs. Once identified, run a cost-benefit analysis comparing ongoing maintenance expenses against replacement value, then work with trusted dealers to time equipment transitions during low-impact project phases to minimize disruption to ongoing work.
For instance, when your 5-year-old skid steer starts needing repairs every month and using 30% more fuel than last year, compare costs: $2,000 monthly repairs versus a $65,000 new machine with warranty coverage. Plan the switch during site cleanup when you have backup equipment available.
Overcoming Challenges in Construction Asset Management
Construction companies face constant pressure to keep their equipment operating efficiently while dealing with multiple obstacles. From unpredictable weather conditions damaging machinery to complicated maintenance timing that can halt entire projects, these challenges can seriously impact both equipment lifespan and project deadlines.
1. Preventing Asset Theft and Misplacement
Construction companies in the UAE report that missing or misplaced equipment can delay projects by 2-3 working days per incident, significantly impacting tight project timelines and budgets in this fast-paced market.[?]
To address these challenges, UAE construction firms are implementing advanced tracking systems aligned with the country's digital transformation initiatives.
For instance, Dubai Smart City vision has encouraged the adoption of IoT-enabled asset tracking, with many sites integrating their systems with Dubai Police's AI-powered security networks.[?]
Major contractors in Abu Dhabi and Dubai are using temperature-resistant GPS trackers and RFID systems specifically designed for the region's climate conditions.
Essential security measures for UAE construction sites include:
-
Integration with local police smart security systems
-
Heat-resistant tracking devices for outdoor equipment
-
Multi-language asset management systems (Arabic/English)
-
Biometric access control suitable for harsh weather conditions
-
Regular coordination with site security teams
2. Managing Asset Depreciation
The UAE construction sector faces a dual challenge: managing equipment degradation in extreme desert conditions while meeting ambitious sustainability targets. This balancing act requires careful planning to maintain both equipment longevity and environmental compliance throughout fast-paced project timelines.
The UAE's emphasis on sustainable construction and modern equipment aligns with local regulations and green building standards like Estidama and Dubai Green Building Regulations.
Companies must consider:
-
Heat stress on equipment (tracking performance drops during peak summer months)
-
Sand/dust exposure impact (using sensors to monitor filter and component degradation)
-
Extended operating hours (logging actual usage hours vs. calendar time)
3. Ensuring Regulatory Compliance
Regulatory compliance in the UAE construction sector is governed by multiple authorities, including municipality regulations, Civil Defense requirements, and Emirates Authority for Standardization and Metrology (ESMA) standards.
Construction companies must navigate both federal and emirate-specific regulations, with Dubai and Abu Dhabi often having additional requirements.
Key compliance areas specific to UAE construction include:
-
Abu Dhabi WorkSafe and Dubai Municipality safety certifications
-
Civil Defense equipment safety requirements
-
ESMA equipment certification standards
-
Green building compliance documentation
-
HSE requirements specific to each emirate
Companies operating in the UAE must maintain documentation in both Arabic and English, with specific requirements for:
-
Equipment registration with local authorities
-
Regular safety inspections aligned with UAE standards
-
Operator certifications recognized by local municipalities
-
Environmental compliance with UAE sustainable development goals
-
Insurance documentation meeting local requirements
The UAE's focus on digital transformation has led to increased adoption of electronic systems for compliance management. Construction firms are increasingly working with government platforms like Dubai Municipality's Al Safat Green Building System and Abu Dhabi's Building Permit Services to streamline their compliance processes.
Best Practices for Successful Construction Asset Management
Whether you're managing a small fleet or extensive construction equipment, understanding and implementing these best practices will help you reduce costly breakdowns, extend equipment life, and ultimately save your company significant time and money.
-
Conduct regular asset evaluations. Schedule and perform quarterly assessments of your construction equipment to prevent unexpected breakdowns and enable better maintenance planning. Through these systematic evaluations, you can collect vital data about equipment performance, which in turn helps you maintain operational efficiency on construction sites and predict future maintenance needs.
-
Understand the value of your equipment. Keep detailed documentation of your equipment's purchase information, usage patterns, and maintenance history. By maintaining these records, you can make informed decisions about repairs versus replacements and ensure optimal resource allocation across your projects, maximizing your return on investment.
-
Inspect your equipment after use. Implement daily post-operation inspection routines to identify potential issues before they become major problems. These regular checks, when conducted systematically with a comprehensive checklist, help prevent unexpected breakdowns during critical project phases and significantly extend equipment lifespan, leading to reduced maintenance costs.
-
Ensure staff are well-trained. Develop comprehensive training programs for equipment operators and maintenance personnel. Through consistent training and regular refresher courses, your staff will become more proficient at identifying potential issues, operating equipment efficiently, and maintaining safety standards on the construction site, resulting in fewer accidents and equipment failures.
Technology Solutions for Effective Asset Management
Construction asset management has evolved significantly with digital transformation, moving from manual tracking to sophisticated technological solutions. While various options exist in the market, choosing the right technology stack is crucial for successful implementation and long-term efficiency.
1. Construction Management Software
Specialized construction management software offers focused solutions for asset tracking, maintenance scheduling, and resource allocation. These platforms typically include features like equipment tracking, maintenance alerts, and utilization reports.
However, while these solutions excel in specific construction tasks, they may lack comprehensive integration capabilities across all business operations. They're ideal for smaller contractors or those focusing primarily on equipment management.
2. Tools for Lead Generation and Tracking
Digital platforms for lead management have become essential in modern construction operations, helping companies identify opportunities and manage client relationships. These tools often include features for tracking potential projects, managing bidding processes, and monitoring market opportunities.
While valuable for business development, these standalone solutions may not directly integrate with asset management systems, potentially creating information silos.
3. ERP Solutions for Integration
Enterprise Resource Planning systems connect all business operations in one platform. For example, FirstBit ERP system manages:
-
Equipment tracking and maintenance
-
Project accounting and costs
-
Resource scheduling
-
Financial reporting
-
Document control
ERP systems cost more upfront but provide the most comprehensive solution for construction companies managing complex operations.
How to Choose the Best Construction Asset Management Software
-
Real-time location tracking. Construction software must show equipment location directly on site maps. GPS tracking prevents lost tools and theft, saves time searching for equipment, and speeds up material deliveries. Teams need instant updates when assets move between project sites.
-
User-training. Pick software with simple interfaces and clear workflows. The system should include training videos, help documentation, and customer support. Your field teams need to learn the basics within 1-2 hours. Avoid complex systems that require extensive training.
-
Tracking maintenance and repair. Software must log equipment hours, schedule maintenance, and track repair costs. Set up automatic maintenance alerts based on hours used or calendar dates. Keep digital records of repairs, parts replaced, and service costs for each piece of equipment.
-
Scalability. Choose software that grows with your business. The system should handle more users, equipment, and projects without performance issues. Check if pricing remains reasonable when adding licenses and features. Verify the software works across multiple project sites.
-
Forecasting availability. The system needs clear calendars showing when equipment is available or reserved. Project managers should easily check equipment schedules 30-90 days ahead. Get alerts about scheduling conflicts and overbooked assets.
-
Ensuring compliance. Your software must store equipment certifications, inspection records, and safety documents. Set automatic reminders for permit renewals and required inspections. Generate reports proving compliance during audits and inspections.
Streamlining Asset Management in Construction with FirstBit ERP
First Bit ERP system manages your construction assets from purchase to disposal. The system tracks each piece of equipment throughout its service life, helping you make the most of your investment.
All equipment paperwork stays organized in one digital location. The system alerts you when warranties or certifications are about to expire, so you never miss important dates.
First Bit shows you clear data about how your equipment is performing and what it costs to maintain. Our system is a solution for you to make better decisions about your construction assets.

Anna Fischer
Construction Content Writer
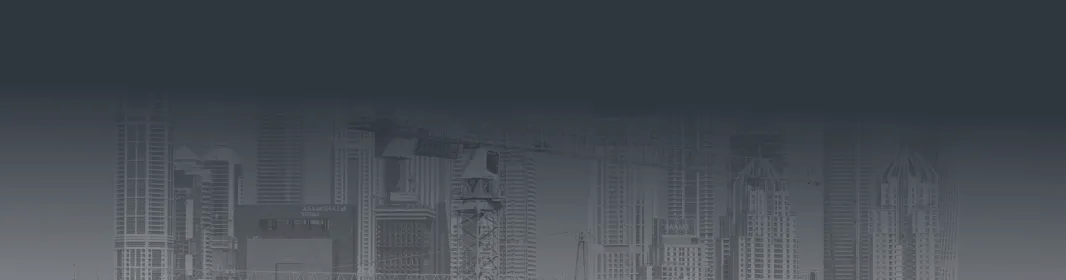
See FirstBit ERP solutions in action
Discover how our system solves the unique challenges of contractors in a personalized demo.
After the demo you will get a quotation for your company.
After the demo you will get a quotation for your company.