Efficiency and cost-effectiveness can make or break a project in the construction industry. One of construction companies' biggest challenges is effectively managing their expensive and complex equipment fleets. From excavators and cranes to generators and hand tools, keeping track of everything, ensuring timely maintenance, and maximizing utilization can feel like a juggling act. This often leads to budget overruns, project delays, and unnecessary downtime.
This article outlines proven strategies for streamlined equipment management designed for construction companies. We'll explore practical ways to improve transparency, increase equipment lifespan, and boost your bottom line.
What is Equipment Management in Construction
Construction equipment is a major investment, and managing it effectively is crucial for project success.
Definition of Equipment Management
Construction equipment management is a systematic approach to overseeing all aspects of a construction fleet, from acquisition and maintenance to operation and training. It involves tracking equipment usage, optimizing its deployment, and scheduling timely maintenance and repairs. This system prioritizes worker safety, manages inventory effectively, and ensures all equipment is backed by proper documentation and comprehensive training.
Implementing these practices in construction equipment management ensures machinery stays in peak operating condition. This contributes to efficient project completion and maximizes the return on investment for each piece of equipment.
Importance of Equipment Management in the Construction Industry
Managing your equipment well is a game-changer for construction businesses. Here’s why it matters:
- Saves money. When you keep up with regular maintenance, your machines are less likely to break down. That means fewer pricey repairs and a longer life for each piece of equipment. Think of it like routine checkups for your car—a little investment upfront saves big in the long run.
- Boosts efficiency. Well-maintained equipment runs better, which means your projects can move faster without unexpected stops. The less you’re dealing with broken machinery, the more you’re able to keep things on schedule, helping you finish projects on time.
- Keeps everyone safe. When your equipment is checked and cared for regularly, it’s safer to use. Fewer breakdowns also mean fewer chances of accidents, so you’re protecting your team and avoiding costly liability issues.
- Maximizes your investment. Equipment is a big-ticket item for any construction business. By keeping it in top shape, you’re getting more bang for your buck and stretching that initial investment as far as possible.
- Simplifies project planning. Knowing your equipment is ready to go makes planning much easier. You can be more confident in your timelines and avoid last-minute delays, which is a big plus for your clients and your bottom line.
Common Challenges in Equipment Management
-
Challenge 1: Equipment breakdowns. Equipment breakdowns interrupt work, leading to delays and increased costs for repairs. Frequent breakdowns can affect project timelines and require contingency planning. Preventive maintenance can help minimize these disruptions but requires organization and foresight.
-
Challenge 2: Rising operational costs. Operational costs, such as fuel, maintenance, and labor, continue to rise, squeezing profit margins. Companies must constantly seek ways to optimize resource use and reduce waste. Effective budgeting and cost management strategies are vital to maintaining profitability.
-
Challenge 3: Inadequate tracking and inventory management. Poor tracking of equipment and inventory can lead to missing tools, redundant purchases, and idle assets. Without a clear system, it becomes difficult to know what equipment is available or needs servicing. Implementing robust inventory management systems can enhance efficiency and reduce waste.
-
Challenge 4: Safety compliance issues. Maintaining safety compliance is crucial but can be complex due to evolving regulations and standards. Failure to comply can result in accidents, legal issues, or financial penalties. Regular training and up-to-date policies help ensure that equipment and operations meet safety requirements.
-
Challenge 5: Difficulty in managing equipment lifecycle. Managing the equipment lifecycle involves understanding when to repair, replace, or retire assets. Without careful planning, companies may face unexpected costs or operational inefficiencies. Lifecycle management strategies help in making informed decisions to optimize equipment use and value.
Choosing the Right Equipment
The right machinery in any construction project can significantly impact project timelines, costs, and overall efficiency. When equipment is well-suited to the specific needs of a job, it leads to smoother workflows and safer job sites. It also often reduces the need for frequent repairs.
For example, using a compact excavator in tight spaces can speed up work and prevent accidental damage that larger equipment might cause. On the other hand, heavy-duty machines like bulldozers or cranes are essential for large-scale projects and moving substantial loads quickly.
Making informed choices about equipment also ensures you're not overspending on machinery that’s more powerful than needed or struggling with equipment that’s too small for the task. Proper equipment selection is about matching the right tool to each job to maximize productivity and get the best return on investment.
Here are some things to keep in mind during your selection process:
-
Assess project needs. Start with identifying the specific requirements and objectives of your project. That’s how you consider the necessary equipment, materials, and human resources to achieve the project's goals.
-
Evaluate site conditions. Analyze the physical and environmental conditions of the project site, such as terrain, climate, and existing infrastructure. This evaluation helps identify any challenges or constraints that could impact the project. Adjusting plans based on site conditions ensures smoother execution and reduces unforeseen issues.
-
Determine your budget. Establish a realistic financial plan by calculating all potential costs, including materials, labor, equipment, and contingencies. A well-defined budget helps in managing expenses and prevents overspending. It acts as a framework for decision-making throughout the project.
-
Research suppliers. Investigate potential suppliers to find those who offer quality products and services at competitive prices. Consider factors like reliability, reputation, and delivery capabilities. Thorough research can lead to finding the best supply options that align with your project’s timeline and budget.
-
Final selection. Make informed decisions on your final choices for suppliers, equipment, and other resources based on your gathered information. Consider all variables, such as cost, quality, and compatibility with project needs. This careful selection process ensures that your project has the best possible support to succeed.
Key Components of Effective Equipment Management
By considering these components in your workflow, you are more likely to extend the life of your construction project.
1. Inventory Management and Tracking
Effective equipment inventory management means knowing what you have, where it is, and how it's being used from the moment you buy it to the day you retire it. This translates to less downtime, higher utilization rates, and smarter purchasing decisions.
Think of it as organizing your toolbox. Instead of rummaging around for the right wrench, you know exactly what's available and where to find it.
Regular checks and updates are crucial. They prevent loss, keep things running smoothly, and ensure you're meeting all compliance standards. Today's tech makes this even easier.
Inventory management software provides real-time tracking, streamlines purchasing, manages suppliers, and generates detailed reports.
2. Maintenance Strategies
A well-defined maintenance strategy is the cornerstone of efficient operations. It maximizes the lifespan of your assets and minimizes costly downtime. It's about shifting from reactive repairs to a proactive approach that keeps your equipment running smoothly. Several strategies exist, each with its own benefits.
-
Preventive maintenance, like routine checkups and scheduled servicing, catches small issues before they become big problems.
-
Predictive maintenance uses data and monitoring to anticipate potential failures, allowing for timely interventions.
-
Reliability-centered maintenance (RCM) dives deep into potential failure modes to determine the most effective maintenance approach.
Choosing the right strategy, or a combination of strategies, depends on your specific needs and the criticality of your equipment.
For instance, consider a construction company managing both high-priority equipment, like a crane needed daily to lift heavy materials, and less-critical machinery, such as a backup generator only used during outages.
The crane is essential to project progress; any downtime directly affects productivity and delays work, so a predictive maintenance strategy, with sensors and frequent monitoring, would be ideal to keep it in top condition. This approach helps catch issues before they lead to a halt in operations, minimizing costly delays.
On the other hand, for the backup generator, which is rarely used, the company might choose preventive maintenance—conducting scheduled checkups every few months to ensure it’s ready when needed. Here, a more intensive strategy like predictive maintenance wouldn’t make sense financially, as the generator’s downtime is less likely to affect daily operations.
In this example, the “needs” relate to how often and intensively equipment is used, while the “criticality” involves how essential each piece of machinery is to the project’s success.
Choosing the right strategy depends on balancing these needs with maintenance costs and ensuring high-impact equipment stays reliable without over-investing in less critical assets.
3. Optimizing Equipment Utilization
Getting the most out of your equipment involves more than just routine maintenance. It requires a strategic approach to how you use it. Operator training and equipment sharing are two powerful ways to boost equipment utilization and, ultimately, your bottom line.
Trained operators know how to handle equipment efficiently and safely. This leads to better performance, fewer breakdowns, and a longer lifespan for your assets.
Equipment sharing is another smart strategy. Instead of letting equipment sit idle, implement a system that allows different teams or departments to share resources. This reduces the need for redundant purchases and saves money.
4. Technology Integration
Connecting and integrating your systems gives you a clear, complete view of your equipment landscape. With this insight, you can make smarter decisions, simplify processes, and boost your bottom line. Technology lets you track equipment in real-time, automate maintenance schedules, and access powerful reporting and analytics—ensuring you get the most value from your assets.
Integrating different software systems, especially an Enterprise Resource Planning (ERP) system, offers a powerful solution for maximizing efficiency and minimizing downtime.
An ERP system acts as a central hub, connecting various departments and functions within your organization. This integration provides a single source of truth for all equipment-related data, from procurement and maintenance records to usage and performance metrics.
A good example is the FirstBit ERP. With FirstBit ERP, you gain a real-time, centralized view of all equipment-related data, from maintenance schedules to performance metrics. For instance, when an excavator is due for maintenance, FirstBit ERP automatically schedules the service and notifies the relevant teams, which prevents unexpected breakdowns on critical projects.
5. Budgeting for Equipment Costs
Consider your equipment budget as the financial roadmap for running your business smoothly. It's not just about buying the shiniest new tools — it's about making smart choices that will save you money in the long run.
A well-crafted budget helps you plan for both upfront costs and those sneaky expenses that pop up down the road, like repairs and maintenance. This means no more financial surprises, just predictable and manageable spending.
A solid equipment budget empowers you to make strategic decisions. Need to upgrade that old machine? Your budget helps you analyze whether buying a new one or giving the old one a little TLC is more cost-effective. It's about getting the most out of your investments and maximizing your resources.
6. Safety and Compliance
Keeping your team and your equipment safe isn't just good practice – it's essential for a successful operation. Think of safety and compliance as the bedrock of effective equipment management.
Just like a car needs regular checkups and maintenance to run smoothly, your equipment needs the same attention to prevent breakdowns and potential accidents. Regular inspections can catch minor issues before they turn into major problems, saving you time, money, and stress in the long run.
But it's not just about ticking boxes on a checklist. It's about creating a culture where everyone understands the importance of safety and feels empowered to speak up if something seems amiss. Clear, easy-to-follow training programs ensure everyone knows how to use equipment safely and responsibly.
When your team feels confident and informed, they're more likely to work carefully and efficiently, reducing the risk of accidents and keeping your operations running smoothly.
7. Sustainability Considerations
Being mindful of our planet is more important than ever, and that includes how we manage our equipment. Think of sustainability as a way to reduce your environmental footprint while often saving money in the process.
One major aspect is choosing energy-efficient equipment. Just like fuel-efficient cars, these machines use less energy, which means lower power bills and fewer emissions released into the environment.
Don't forget about the end life of your equipment. Instead of sending old machines to a landfill, explore options like reselling, donating, or even having parts recycled. This keeps valuable materials in circulation and out of landfills.
Finally, think about your maintenance routines. Using eco-friendly cleaning products and properly disposing of hazardous materials like oils and batteries shows your commitment to a healthier planet.
Best Practices for Equipment Management
Pay attention to these practices if you want to streamline your construction project processes.
1. Develop a Clear Equipment Management Strategy
Start by defining your goals for equipment management. Are you aiming to cut costs, increase uptime, or extend asset life? Based on these goals, create specific guidelines covering procurement, operation, and maintenance.
For instance, set criteria for purchasing equipment, such as budget limits or specific performance features, and establish clear usage protocols to prevent unnecessary wear and tear.
Implement a maintenance schedule that ensures regular check-ups based on hours used or project type. This structure helps streamline operations and ensures everyone follows the same playbook.
2. Implement a Lifecycle Management Approach
Think of each piece of equipment as an asset with a lifecycle. Track everything from the purchase date, usage patterns, and maintenance history to eventual disposal.
To do this, set up a log or digital record that includes maintenance checklists, repair costs, and any upgrades. By closely monitoring this information, you can decide the best time to replace equipment before repair costs outweigh the benefits.
Additionally, a lifecycle approach ensures you get the most out of your equipment without unexpected costs or downtime disrupting your project.
3. Opt for Data-Driven Decision Making
Instead of relying on estimates or gut feelings, leverage data to make informed decisions. Set up performance metrics, such as fuel consumption, operating hours, and downtime frequency, and review these regularly.
Use this data to identify trends—like if a specific machine consistently requires repairs after a certain usage threshold. This insight helps determine whether to repair, replace, or upgrade. Tracking this data might require software solutions that consolidate information across projects, allowing you to spot inefficiencies and improve asset utilization.
4. Encourage Cross-Department Collaboration
Effective equipment management requires strong collaboration among departments. Maintenance teams, for example, should keep operations informed about equipment availability while finance tracks costs and budgeting for repairs or replacements.
To foster this communication, establish a regular check-in process or use a shared digital platform where departments can update equipment status, share maintenance needs, and manage costs in real time. By having everyone on the same page, you avoid overuse or downtime caused by miscommunication.
5. Regularly Review Processes and Performance
Conduct periodic reviews to assess how well your equipment management strategies are working. Set a monthly or quarterly time to evaluate metrics, like maintenance costs, downtime, and usage rates.
Ask key questions: Are maintenance costs increasing? Is downtime affecting project timelines?
Use this review to spot areas for improvement, such as adjusting maintenance frequency or reallocating equipment across projects. Regular reviews allow you to refine your processes, keep equipment in top shape, and adapt to project demands.
6. Automate Processes Using an ERP Software
Automation can save time by handling tasks like scheduling maintenance reminders and tracking equipment usage. An ERP system like FirstBit can automate several aspects of equipment management, saving time and reducing errors.
Set up automatic reminders for maintenance, track equipment usage across projects, and access real-time performance data. This automation means fewer manual entries and fewer missed check-ups, ultimately leading to better-managed assets and fewer unexpected breakdowns.
How to Optimize Equipment Management with FirstBit ERP Software
Think of FirstBit ERP software as a command center for your equipment. It helps you keep track of everything in one place, making management a breeze. Here's how it helps you optimize your equipment:
-
You can track equipment management from this screen. It allows you to see who manages the equipment, what equipment is being used, and how long someone has been using it.
-
You can create notifications to remind you to check equipment and prevent breakdowns by this report.
-
Track equipment costs, including purchase price, maintenance expenses, and depreciation. This data helps you make informed decisions about repairs, replacements, and overall budget allocation.
FirstBit ERP empowers you to take control of your equipment and improve your bottom line. Rather than waiting for breakdowns, you can proactively schedule maintenance, ensuring your operations run smoothly and preventing costly downtime.

Anna Fischer
Construction Content Writer
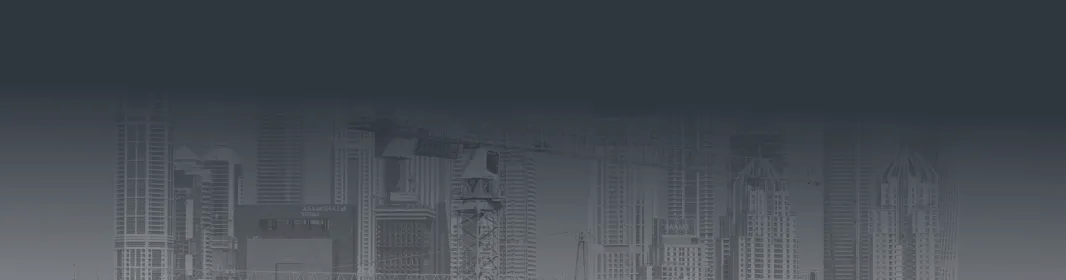
See FirstBit ERP solutions in action
Discover how our system solves the unique challenges of contractors in a personalized demo.
After the demo you will get a quotation for your company.
After the demo you will get a quotation for your company.