In the construction industry, managing labor costs is crucial for the success of a project's budget. Contractors and project managers often face challenges in overseeing a diverse and changing workforce, coordinating labor across multiple project sites, and maintaining operational efficiency. Outdated labor management systems result in data inaccuracies and make it difficult to comply with labor regulations, which leads to inefficiencies and increased costs. This creates significant challenges for those responsible for project budgets.
If you are looking for ways to effectively manage labor costs, this article offers insights and practical strategies to optimize labor costing in construction. You’ll also learn how to calculate labor cost in construction for better budgeting each quarter. Understanding and implementing effective labor cost management techniques can enhance your operational efficiency and maintain control over your project budgets.
The Role of Labor Costs in Construction Projects
Labour expenses usually include:
-
training
-
onboarding
-
paid time off
-
benefits like social security and workers' compensation
-
payroll taxes
The shortage of construction workers complicates labor costs, as companies now have to compete more to find skilled workers.
Labor costs typically contribute 30-50% of the total construction cost of a building, and this figure can be even higher depending on the type of building.[?]
Labor costs play a crucial role in construction in the following ways:
-
Major part of the budget. Labor costs often make up a big chunk of the total cost of a construction project. If not managed carefully, they can quickly add up, making the project more expensive than planned.
-
Direct impact on project timelines. If you don't have enough workers or if they are paid poorly and decide to leave, it can slow down the work, causing delays. On the other hand, hiring too many workers can also waste money if they are not needed.
-
Skill and availability matter. Construction projects need a mix of skilled and unskilled workers. Sometimes, there may be a shortage of skilled workers, which drives their wages as companies compete to hire them. This can unexpectedly increase labor costs.
-
Affects overall profit. If labor costs are too high or poorly managed, the company's profit will be reduced. Keeping these costs in control helps ensure the project's profitability.
Understanding Construction Labor Costs
Labor costs are a major part of a construction company's expenses and can be divided into direct and indirect costs. Each type plays a specific role in the production process and overall business operations.
1. Direct Construction Labor Costs
Calculate construction labor costs accurately by considering:
Wages and Salaries. In construction businesses and similar operations, direct costs refer to the wages paid to workers directly involved in a particular project. These wages are attributed to direct labor costs tied to specific project tasks. For example, the wages of carpenters, electricians, and other specific tradespeople working on a project are considered direct costs.
It's important to note that not all wages and salaries are considered direct costs. Some employees, such as supervisors or administrative staff, work on multiple projects or perform duties that benefit the entire business.
Their wages are not specifically attributed to a single project, so they are considered indirect or overhead costs. While wages for direct labor are a significant part of direct costs, it's crucial to distinguish them from salaries that support general business operations, which are considered indirect costs.
Benefits and Bonuses. Legally mandated benefits like social security and workers' compensation, along with commonly offered perks like health insurance and retirement plans, can significantly increase overall labor costs. Bonuses tied to project milestones, individual performance, or employee retention further add to these expenditures.
Overtime Pay. Workers in the UAE are entitled to overtime pay at a rate of at least 1.25 times the regular rate if they work more than 48 hours in a week. UAE Labor Law provides for paid leave on public holidays. If workers are required to work on these holidays, they are entitled to either a compensatory day off or additional pay for that day (1.5 times the regular rate).
Training and Certification.Training and certification are important direct costs in the construction industry. They are essential investments in workforce competency and compliance with industry standards. These costs are directly associated with specific projects and include fees for certification programs and wages paid to employees during training. These investments are crucial for ensuring that workers are skilled and certified, which can lead to increased productivity and reduced on-site accidents.
2. Indirect Construction Labor Costs
Supervisory and Management Personnel. Supervisory and management personnel oversee operations to ensure that projects run smoothly and efficiently. This group includes project managers, site supervisors, safety managers, and departmental heads. While they play a critical role in coordinating work and managing resources, their work is not directly tied to the output of specific projects.
Safety and Quality Assurance. Safety expenses may include salaries for safety officers, costs of safety training sessions, personal protective equipment (PPE), and safety audits. Quality assurance (QA) involves systematic processes to ensure construction work meets specified standards. This includes inspections, testing materials, and compliance checks.
Support Staff. Support staff is also an indirect cost, as it cannot be directly linked to a company's revenue or profit but contributes to other functions that improve the business's overall productivity. These include positions such as human resources manager, administrative staff, CEOs, maintenance and repair workers and many others. Employees in these positions usually have fixed expenses, but may sometimes vary according to production output.
A Step-by-Step Guide to Accurately Calculating Labor Costs
Knowing how much money you spend on labor ensures that you avoid overspending and can make informed decisions about where to allocate funds.
Task-by-Task Cost Estimation
Estimating construction costs on a task-by-task basis is a detailed approach that involves breaking down a project into individual work items, so you can calculate labor cost for each task.
-
Create a work breakdown structure (WBS). Divide the project into manageable tasks and subtasks. Manageable tasks refer to broader work items that represent significant deliverables or milestones within a project. Subtasks are smaller, more specific actions that fall under a manageable task.
-
They break down the larger task into detailed steps, making it easier to manage and track progress. You can also group tasks together to create a hierarchical structure.
-
Estimate hours required for each task. Determine the appropriate labor rates for each type of worker (e.g., carpenters, electricians, plumbers) based on their skills and experience. Estimate the labor hours required for each task based on historical data, industry standards, or input from experienced personnel.
-
Add up costs. After estimating the hours for each task, calculate construction labor costs. This process includes direct labor costs, materials, equipment, and overhead costs for each task. Multiply the estimated hours by the labor rate, add material and equipment costs, and include a percentage for overheads. Don't forget to factor in labor burden costs, such as payroll taxes, benefits, and insurance.
For example, break down the project into manageable tasks such as foundation, framing, electrical, plumbing, and finishing. Each task can be further divided into subtasks; for example, under framing, there is floor framing, wall framing, and roof framing.
Unit Pricing Method (Cost per Unit)
Businesses use unit pricing to calculate the cost of a single product for customers.
The unit cost formula helps you figure out how much it costs to make one item. The formula is:
Cost per unit = variable cost + fixed costs / total units produced.
Determining the unit price for a product helps companies make better profitability decisions and informs consumers about the product's worth.
Suppose you're building a warehouse with variable costs (such as materials and labor) totaling 180,000 AED and fixed costs (such as permits and equipment rentals) of 70,000 AED. If you are constructing five identical warehouses, you can calculate the cost per unit as follows:
-
Add up the variable costs: 180,000 AED
-
Add the fixed costs: 70,000 AED
-
Find the total cost: 180,000 AED + 70,000 AED = 250,000 AED
-
Divide by the number of units (warehouses): 250,000 AED / 5
Thus, it costs 50,000 AED to build each warehouse.
Square Foot Method
Estimating square footage is a common method used in construction to calculate the cost of a project based on the total area of the space being built or renovated. This method involves multiplying the total square footage by a set unit cost to provide an initial assessment of the overall expense. [?] This also lets stakeholders know the approximate project cost before conducting a detailed cost analysis.
The square footage method is especially helpful in the initial phases of a construction project when detailed plans may not be available. Offering a rough estimate assists project managers and clients in making informed decisions regarding budgeting and feasibility.
The square foot method of estimating typically involves the following steps:
-
Begin by measuring the total area, including all interior and exterior spaces, to be constructed or renovated in square feet.
-
To determine the cost per square foot, consider factors such as the type of project (new construction or renovation), the intended use of the structure, the materials and labor rates, the location, and the size requirements of the structure (e.g., area, number of stories, and story height). Keep in mind that this cost will vary based on the specific requirements of your project.
-
Multiply the total square footage by the cost per square foot to obtain an estimated total project cost. This preliminary budgetary figure will provide guidance for decision-making and planning.
-
Refine the estimate by adjusting the cost based on factors such as site conditions, design changes, material selections, and market fluctuations. These adjustments ensure accuracy.
Cost estimates may not consider all the factors like materials, labor costs, and site-specific challenges. To ensure accuracy and avoid exceeding the budget, you can use more detailed cost estimation methods as the project progresses.
4. Rule of Two Method
The "rule of two" is a simple way to estimate labor and material costs by assuming labor typically makes up 30-50% of the total project cost. It works by estimating the labor cost, then multiplying it by two to get a rough total cost. This method is based on experience rather than actual data and assumes a project will take a certain amount of time.
To calculate labor cost, multiply the estimated hours by the hourly rate and then double the result.
If 5 workers work 8 hours each at AED 20 per hour, the labor cost would be: (5 x 8 x AED 20) x 2 = AED 1,600
You can then add 10-15% for incidental expenses, bringing the labor cost to AED 1,840.
Although the rule of two gives a quick estimate, it shouldn't be the only method used. It doesn't consider real costs, cash flow needs, or changing project conditions.
Key Factors Affecting Labor Costs
Start by examining these underlying factors to find ways to control your expenses.
1. Shortage of Skilled Workers
-
Due to a shortage of skilled labor, employers often need to raise wages to attract and retain qualified workers.
-
When skilled workers are scarce, existing employees may need to work overtime to meet project deadlines. In the UAE, overtime pay is the regular hourly rate plus 25%. It increases to 50% for hours worked between 10 PM and 4 AM.
-
Companies may hire less qualified or inexperienced workers in response to labor shortages, leading to lower productivity and increased errors.
-
Employers may need to invest more in training programs for new hires lacking the necessary skills to calculate labor costs accurately and plan budgets effectively.
2. Safety and Health Expenses
-
Employers often invest significantly in safety training, equipment, and protocols to prevent workplace injuries.
-
The costs associated with purchasing personal protective equipment (PPE) such as helmets, gloves, and safety glasses also contribute directly to labor costs.
-
When accidents occur, employers face direct costs from workers' compensation claims.
-
Construction companies that fail to meet safety regulations face penalties that can be substantial.
3. Challenges with Technology Adoption
Although technology like ERP systems and accounting software can be beneficial, several challenges can delay its implementation, which can result in higher labor costs.
-
High initial costs. When new technologies are introduced, productivity might drop at first as workers adjust to the new systems. This slowdown can temporarily raise labor costs since projects may take longer than expected.
-
Resistance to change. The construction industry has long depended on manual methods and established routines. Many workers may hesitate to adopt new technologies, fearing job loss or changes to their usual way of working.
-
Skills gap. The construction industry faces difficulty attracting younger workers who are comfortable with technology. Without tech-savvy employees, companies may struggle to use modern tools effectively.
-
Impact on productivity. During the transition to new technologies, productivity might drop at first as workers learn the new systems. This slowdown can cause higher labor costs because projects may take longer than expected to finish.
4. Compliance With Labor Regulations
Compliance with labor regulations is a significant factor that affects labor costs across various industries, including construction. These regulations encompass a wide range of requirements related to worker safety, wage standards, benefits, and workplace rights. Here’s how compliance impacts labor costs:
-
Businesses often incur direct costs associated with ensuring compliance with labor regulations. Research indicates that firms spend between 1.3% and 3.3% of their total wage bill on regulatory compliance tasks. This includes costs for hiring compliance officers, conducting audits, and maintaining necessary documentation.[?]
-
Employers must invest in training programs to ensure that employees understand their rights and responsibilities under labor laws. This training can be costly, particularly in industries with complex regulations.
-
Compliance requires significant administrative effort to track hours worked, manage payroll accurately, and maintain records in accordance with regulations. Studies have shown that compliance-related tasks can account for over 20% of total labor input in some industries, leading to increased labor costs due to the time spent on these activities.[?]
-
Non-compliance with labor regulations can result in substantial fines and penalties, which can significantly impact a firm's financial health. For instance, failure to comply with wage laws or safety regulations can lead to costly legal battles and settlements.
5. Rising Wage and Benefit Costs
-
Rising wage and benefit costs are critical factors significantly affecting labor costs in construction, including the UAE. In Dubai, the compensation value for building construction workers reached approximately 9.6 million AED in 2020.[?]
-
Moreover, the UAE's total number of construction workers surged to nearly 1.6 million by 2021, highlighting substantial workforce growth. Wage structures in the UAE have been subject to agreements between employers and employees, with basic wages often constituting 50% to 60% of the total salary.[?]
With these financial pressures, contractors must effectively manage and anticipate rising labor costs, while also being able to calculate costs precisely. All of this is necessary to maintain profitability and competitiveness in the booming UAE construction sector.
Strategies for Managing and Reducing Labor Costs
These strategies will help you manage and reduce labor costs, thereby improving your organization's overall financial health.
1. Plan and Schedule Wisely
In every construction business, it is crucial to streamline and manage the workflow schedule effectively.
First, ensure that workflow charts have realistic goals and well-defined schedules. Explain the nature of the work and assign laborers to subgroups.
Make sure that the workflow schedule clearly defines the time for each task to be completed. Match the progress of your construction crew with the workflow schedule chart each day. Discuss and ask for feedback from leaders to make necessary changes to streamline the workflow schedule.
2. Outsource or Keep In-House
Choosing between outsourcing and keeping operations in-house is a critical strategic decision that can significantly impact labor costs and overall business efficiency.
Outsourcing
Construction outsourcing refers to hiring third-party companies or individuals to perform tasks, handle operations, or provide services that might otherwise be carried out by in-house staff. These outsourced parties can include specialized contractors, consultants, engineering firms, and suppliers. Outsourcing minimizes employee-related expenses and provides operational flexibility to adjust swiftly as per project demands.
However, outsourcing can lessen control over processes and quality, with diverging time zones and communication issues potentially adding to the challenge. The quality of work may fluctuate depending on the outsourcing team's skills and standards.
Keeping In-House
Managing construction projects in-house involves handling tasks internally rather than outsourcing to third parties. This approach provides greater control over project timelines, ensuring full utilization of internal resources.
Nevertheless, if specific skills are required that are not currently available within the team, companies may need to invest in training or hiring new staff, which can delay projects and increase costs.
A hybrid approach that combines both strategies might be the most effective way to manage labor costs while leveraging the strengths of each model. By carefully analyzing the nature of the tasks involved—whether they are core competencies or non-core activities— companies can make informed decisions that optimize their labor cost management strategies.
Invest in Training
Consider strategically investing in training to enhance efficiency and boost your bottom line. Here’s how smart training investments can transform cost management in your construction business:
-
Skill up. Equip your team with cutting-edge skills to ensure tasks are completed correctly the first time.
-
Accelerate onboarding. Streamline the onboarding process with targeted training programs.
-
Adopt new technologies. Train employees on the latest construction technologies like ERP systems and methodologies that can speed up project timelines and reduce labor hours.
-
Regulatory training. Regular compliance training minimizes the risk of costly fines and project shutdowns due to regulatory violations.
Use Technology and Automation
Implementing technology and automation in your construction projects is a game-changer for reducing labor costs. Here’s how leveraging these tools can transform your operations:
-
Streamline processes. Use automation for repetitive tasks, allowing your crew to focus on high-skill activities.
-
Enhance accuracy. Deploy advanced tech to minimize errors and rework.
-
ERP systems. Integrate ERP systems to optimize project management, supply chain, and financial tracking.
-
Real-time analytics. Utilize tools that offer real-time data for decision-making and better resource allocation.
-
Mobile solutions. Equip teams with mobile technologies to access information on the go, boosting productivity and reducing downtime.
FirstBit ERP: A Solution for Managing Labor Costs in Construction
-
Cash flow management. With the help of FirstBit construction project cost control software, construction managers can get a complete overview of cash flow for all ongoing projects. This overview enables precise tracking of labor expenditures and aids in forecasting future cash flow needs. As a result, it ensures that there are enough funds available to cover labor costs without any delays.
-
Procurement and billing. The FirstBit ERP System consolidates all Bills of Quantities (BOQs), sales receipts, and invoices into one accessible platform. This centralized tracking and matching process helps determine profitability, ensures accurate accounting, and optimizes procurement processes, leading to more efficient labor cost management.
-
Project cost control. The FirstBit ERP enables real-time cost monitoring, allowing for prompt implementation of control measures. Detailed tracking of Bill of Quantities (BOQ) items from request to receipt helps prevent unexpected costs and labor overruns, thus maintaining budgets and reducing waste.
-
Project estimating and budget. FirstBit enables the import of BOQ to create accurate project estimates and budgets. Managers can set up detailed labor budgets for each project and use these estimates for multiple projects.
Southern Interiors LLC faced challenges managing day-to-day operations before implementing FirstBit ERP. They used multiple software programs, leading to data entry issues and inaccurate reporting. The decision to implement FirstBit ERP was driven by its advanced functionality and customer-centric approach.
With the new system, the company has experienced improved report generation, clearer project monitoring, and a reduction in human error. This transformation has been particularly beneficial in managing labor costs more effectively, leading to greater overall efficiency and productivity.
FAQ
1. What is the meaning of rising labor costs?
2. How to calculate labor costs?
3. How do you estimate labor costs for construction?
4. What is a normal labor cost?

Anna Fischer
Construction Content Writer
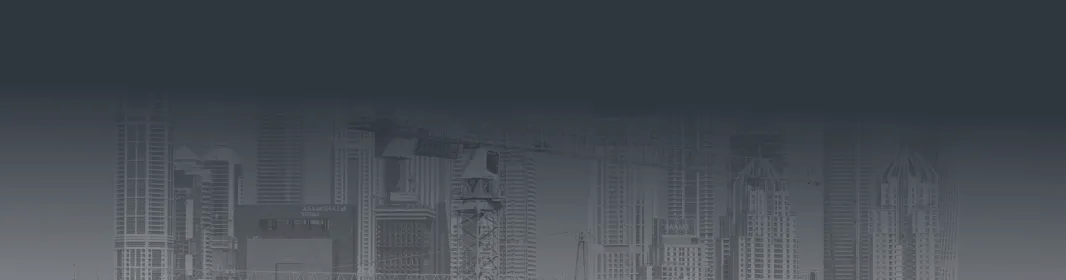
See FirstBit ERP solutions in action
Discover how our system solves the unique challenges of contractors in a personalized demo.
After the demo you will get a quotation for your company.
After the demo you will get a quotation for your company.