Understanding Subcontracting in Construction
1. Who Is a Subcontractor?
2. Types of Subcontractors in Construction: Who Does What?
-
Site preparation subcontractors. Before the building starts, some general contractors bring in experts to prepare the site. These experts use big machines to make a driveway, cut down trees, flatten the land, and dig space for the foundation. Sometimes, the concrete expert might hire another company to prepare the site.
-
Concrete subcontractors. Concrete subcontractors are the experts who handle all the concrete work on a building site. They're responsible for pouring foundations, footings, and other concrete structures. These specialists usually work directly with the general contractor to lay the groundwork for the project. Their job doesn't stop at the foundation, though. Once the main building is finished, they might also create concrete driveways, walkways, and patios.
-
Structural and framing subcontractors. Buildings can be made from different materials like wood, steel, or concrete. You can hire a team just for framing. These workers put up the basic structure for walls and roofs. The framing team might also put on the outside covering of the building, add windows, and install outside doors.
-
Electrical. Every job site needs electrical subcontractors. They install all electrical items you can't legally handle, like panels, wires, and fixtures. For new builds or big renovations, they also set up temporary power. Electricians work with all trades and use various plans to coordinate their work properly.
-
Plumbing. Plumbing subcontractors manage water flow in buildings, installing systems for clean water intake and wastewater removal. They set up waste lines, vents, and water pipes during construction or renovations. Plumbers also connect to external water sources like city mains or wells. You can hire them directly for septic system development. Mechanical subcontractors often handle plumbing and HVAC and gas services for larger projects because they offer a more comprehensive approach.
-
HVAC. Heating, Ventilation, and Air Conditioning subcontractors play a key role in the maintenance of safe and comfortable indoor environments for building occupants. The complex nature of interior climate control requires specialized expertise and experience, making it essential to entrust this task to qualified HVAC professionals. HVAC subcontractors install and maintain various equipment, such as boilers, furnaces, ductwork, and air conditioning units, all designed to optimize building comfort.
3. Must-Have Skills for Successful Subcontractor Management
Successful construction projects rely on effective collaboration among skilled professionals. Proficient subcontractor management often determines whether a project succeeds or encounters difficulties.These eight skills will help you effectively manage your subcontractors:-
Clear communication. Talk clearly and regularly with your subcontractors. Set clear expectations, give feedback, and answer their questions promptly.
-
Thorough documentation. Keep detailed records of everything related to subcontractor work. This includes contracts, invoices, and any other important paperwork.
-
Negotiation. This includes payment schedules, deadlines, and other important details. Approach negotiations with a clear understanding of the project's scope, budget, and priorities to establish fair agreements. Build rapport with subcontractors by demonstrating flexibility where possible while maintaining firm adherence to the project's key objectives to ensure mutual satisfaction and compliance.
-
Risk management. Subcontractors can introduce risks to a project. Common risks include delays, poor quality work, and non-compliance with regulations. Identify and manage these risks to keep the project on track. To identify risks, conduct thorough pre-qualification checks, review subcontractors' past performance, and monitor their compliance with project requirements. Manage these by setting clear expectations, performing regular inspections, and maintaining open communication to address issues promptly and collaboratively. Establishing contingency plans can further mitigate potential disruptions, ensuring the project progresses smoothly despite unforeseen challenges.
-
Quality control. Ensure quality work by setting standards, monitoring performance, and providing regular feedback to your subcontractors.
-
Conflict resolution. Disagreements can happen. Have the process resolution process in place to quickly and fairly resolve conflicts with subcontractors. Talk openly and use a neutral person to help solve disagreements quickly. Ensure all agreements are documented in writing, and set regular check-ins to address any concerns before they escalate.
-
Performance evaluation. Regularly evaluate how your subcontractors are performing. Set goals, track progress, and give feedback to help them improve.
-
Cost management. Keep costs under control. Set budgets, track expenses, and negotiate fair prices with your subcontractors. Use cost-tracking tools to monitor spending in real time and tie payments to project milestones to maintain financial control. Review costs regularly, address overruns promptly, and maintain transparent communication with subcontractors to ensure accountability and prevent financial discrepancies.
-
Why Effective Subcontractor Management is Key to Construction Project Success
Example: Imagine a construction project where the general contractor fails to properly coordinate the electrical and plumbing subcontractors. The electricians install wiring based on the original blueprints. However, the plumbing subcontractor, working from a slightly revised plan, installs pipes in a location that conflicts with the wiring. Because the general contractor didn't check for coordination between the two subcontractors or ensure they were using the latest plans, this clash wasn't discovered until the drywall was almost finished.
1. Project Timelines and Deadlines
Example: The construction of the Burj Khalifa in Dubai, completed in 2010, exemplifies how effective subcontractor management ensures timely project completion. The general contractor, Samsung C&T, carefully selected subcontractors with the necessary expertise and employed advanced planning and scheduling tools to coordinate their efforts. Regular meetings were held to align goals and address potential delays, while on-site management ensured quality control. Precise logistical planning facilitated the global sourcing and timely delivery of materials. These strategies allowed the Burj Khalifa to be completed in just six years.[?]
2. Cost Management and Profitability
Example: The Sydney Opera House project, although initially plagued by cost overruns, serves as an example of how careful subcontractor selection, competitive bidding, and efficient change order management can help control costs. As the project progressed, the management team focused on selecting subcontractors with the necessary expertise and conducted competitive bidding to ensure value for money. They also implemented efficient change order management to address design changes and unexpected conditions, mitigating unnecessary expenses.[?]
3. Quality Assurance and Reputation
Example: The construction of The Shard in London demonstrates how clear quality standards, regular inspections, and a strong quality control process ensure excellent workmanship and protect a project's reputation. Due to Renzo Piano's precise architectural design, the team set clear quality benchmarks from the start. Routine inspections helped quickly spot and correct any issues, while a dedicated quality control team ensured all work met strict standards, ensuring high-quality results throughout the project.[?]
4. Safety Compliance and Risk Mitigation
Example: The construction of the Louvre Abu Dhabi in the UAE is a great example of how careful planning can reduce safety risks and legal problems. The project involved a complex dome design, requiring close coordination among contractors. To maintain safety, the team chose subcontractors (Arabtec and Bauer International FZE) with excellent safety records and insurance coverage. Special safety measures were also developed due to the site's proximity to water and design challenges.[?]
5. Enhanced Coordination and Communication
Example: During the construction of One World Trade Center in New York City, effective communication and collaboration were key to the project's success. The general contractor used advanced project management software to ensure that all stakeholders, including subcontractors, had access to real-time updates and documents. Regular on-site meetings and weekly progress reviews facilitated immediate issue resolution and aligned everyone on goals and timelines. Additionally, using tools like Building Information Modeling (BIM) allowed different teams to visualize and collaborate efficiently, helping resolve issues before they arose on-site.[?]
Manage teams, equipment, and materials in FirstBit
Common Challenges in Subcontractor Management
1. Lack of Analytics and Reporting
According to Rob Norton, the Director of PlanRadar, nearly two-thirds (60%) of general contractors feel they don’t receive enough information from subcontractors to provide complete project oversight.
2. Ineffective Communication Channels
Rob Norton notes that eight in 10 (80%) have experienced misunderstandings and disputes due to a breakdown in communication with subcontractors.
3. Data Inaccuracy and Security Risks
4. Weak Subcontractor Relationships
5. Budget Management Issues
6. Safety and Compliance Standards
7. Staff Training Gaps
Traditional vs. Digital Subcontractor Management: Which Approach Is More Efficient?
1. Traditional Methods
2. Digital Methods
-
Real-time updates. Instantly see the project progress and address issues quickly.
-
Improved communication. Streamlined communication channels keep everyone on the same page.
-
Better data integration. Connect different parts of your project for a complete overview.
-
Enhanced accuracy. Reduce errors and improve data quality.
-
Increased efficiency. Automate tasks and free up valuable time.
Features of a High-Performance Subcontractor Management System
-
Real-time collaboration tools. These tools, like instant messaging and project management platforms, keep everyone on the same page. For example, if a delay occurs, the subcontractor can immediately inform the project manager, preventing costly ripple effects. This constant communication fosters transparency and quick problem-solving.
-
Document storage and sharing. Centralized storage for contracts, safety documents, and schedules ensures everyone has access to the latest versions. Imagine needing a specific safety certificate during an inspection – with centralized storage; you can access it instantly, avoiding delays and demonstrating compliance.
-
Progress tracking and task assignment. This feature allows project managers to monitor milestones and stay updated on subcontractor work. For instance, if a subcontractor falls behind on their tasks, the project manager can intervene early, adjust schedules, and prevent major delays down the line.
-
Payroll integration. Automating payments based on completed work saves time and reduces errors. Instead of manually processing invoices, the system automatically calculates payments based on verified progress, ensuring accurate and timely compensation for subcontractors.
-
Compliance and certification tracking. Monitoring certifications and safety compliance is crucial to avoid legal issues. The system can track expiry dates of safety certifications and alert you in advance, allowing time for renewals and preventing potential work stoppages.
-
Automated alerts and notifications. Automated alerts for missed deadlines or upcoming renewals keep projects on track. For example, an alert can notify the project manager if a subcontractor misses a key deadline, prompting immediate action and minimizing delays.
-
Analytics and reporting. Detailed reports on subcontractor performance provide valuable insights. By analyzing past performance data, project managers can identify reliable subcontractors, pinpoint areas for improvement, and make informed decisions for future projects.
Transform Subcontractor Management with FirstBit ERP: A Solution Built for Construction
-
FirstBit ERP streamlines construction project management with its real-time features. Project managers can instantly monitor subcontractor performance while the system provides a clear overview of each project's status, budget, and resources at a glance.
-
Our system makes document management and compliance tracking easier for you. It provides a central place to store all project documents, making them easy to find and update. The ERP system also helps track compliance requirements, alerting teams about upcoming deadlines. This organized approach reduces mistakes, saves time, and keeps projects running smoothly.
-
FirstBit ERP is a great tool for you to make transactions quickly. The system links invoices directly to project progress, ensuring more accurate billing. This improves cash flow management and helps keep the project's finances on track. With our system, you can trust that financial records are up-to-date and error-free.
Assign the right people to the right tasks

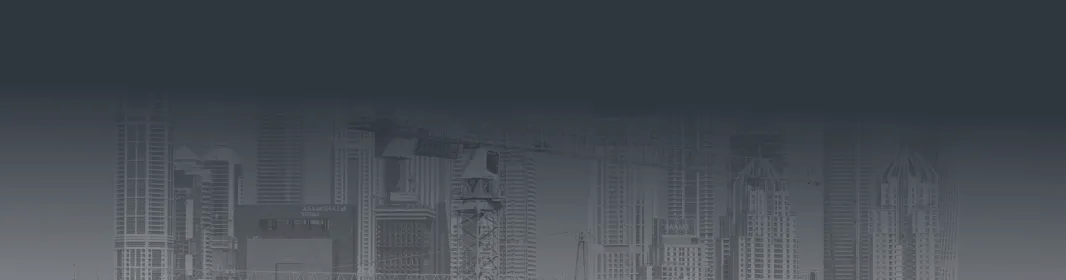
See FirstBit ERP solutions in action
After the demo you will get a quotation for your company.