If your business depends on warehouses for supply chain management, multiple challenges are inevitable, especially if you conduct manual workflows. There is always a high risk of human error and inefficiency in handling large volumes of inventory, which can lead to delays and inaccuracies in order fulfillment.
One of the must-have solutions for you is a Warehouse Management System (WMS). In this article, you will learn how implementing a WMS can streamline operations, reduce costs, and improve inventory accuracy and efficiency in your warehouse.
Understanding the Meaning of WMS
A warehouse management system is software that supports and optimizes warehouse functionality and distribution center management. These systems facilitate the control and management of daily operations from when goods or materials enter a warehouse until they move out.
The system streamlines all warehouse management activities through a single interface, covering aspects from receiving and put-away to inventory tracking and replenishment. Additionally, the WMS system integrates with other technological tools, such as bar code scanning, RFID labeling, advanced robotics, augmented reality (AR) wearables, and vital business systems like transportation management systems (TMS), enterprise resource planning (ERP), and other logistics software.
This comprehensive framework ensures that warehouses respond effectively to shifting demand dynamics while maintaining efficiency and meeting modern logistical challenges.
Where Does WMS Fit Into the Supply Chain?
A warehouse is the place where materials and inventory are delivered, stored, and transported from, forming an essential part of the supply chain. A Warehouse Management System (WMS) makes this chain work effectively by tracking everything digitally, ensuring no materials are lost, and preventing delays. It keeps each item visible by showing when something will be delivered and where it is currently located. This real-time data helps businesses make the right and timely decisions about what to buy and when to transport items, ensuring smooth and efficient supply chain operations.
Why Do Businesses Today Need a WMS?
If your business is struggling with warehouse management, a WMS can address those challenges. Let's explore how it works.
Inventory and Shipping Monitoring
Warehouse management systems provide inventory and shipping data access, which enables businesses to identify bottlenecks and delays:
-
Difficulties with carriers. Businesses often face delays in coordinating shipments due to poor communication with carriers, leading to scheduling conflicts, missed delivery windows, and increased transportation costs. These issues can disrupt the entire supply chain.
-
Handling returns. Managing returns can quickly become chaotic without a system in place to track them. Without the aid of WMS for inspection, it's difficult to efficiently allocate returned items for restocking, repair, recycling, or disposal. Manual inspections also significantly delay the availability of items for resale.
-
No real time tracking. The absence of the real time tracking feature can cause delays in tracking shipments and in predicting their arrival times. Furthermore, the potential for goods to get lost in the shipping process can negatively affect both the business operations and customer service.
With features like automated alerts, real-time tracking, and centralized data management, a WMS ensures that both warehouse staff and carriers are aligned, reducing the likelihood of delays and optimizing delivery routes.
Customer Service Issues
Customers demand transparency and reliability in tracking their shipments. The following points are essential in ensuring that your customers remain satisfied:
-
High order accuracy so your customers do not get the wrong products
-
Faster order fulfillment without unnecessary delays
-
Accurate tracking information to keep the customer updated on the delivery of their order
-
Smoother return process to keep customers believing in your service
Achieving these tasks through manual workflows is difficult and often leads to errors and inefficiencies. Warehouse management systems streamline these processes, enhancing customer service.
Competitive Edge
Businesses today face several key challenges in maintaining a competitive edge in the warehouse management landscape:
-
Customer expectations for faster and more accurate order fulfillment are higher than ever.
-
Managing a large and diverse inventory efficiently has become increasingly complex.
-
Operational inefficiencies and reliance on manual processes can lead to higher costs and slower order fulfillment times.
-
Effective coordination with suppliers and other parts of the supply chain is crucial for smooth operations. Making informed decisions in real time is essential for maintaining competitiveness, yet it can be challenging without comprehensive data.
As businesses grow, their operational needs become more complex, requiring scalable and flexible solutions to handle increased volumes and new challenges. A WMS offers solutions to all of these challenges to help your business stay competitive.
Additionally, with almost every business automating processes using a WMS, it’s no longer an opportunity but a core requirement in order to not lag behind.
Benefits of Implementing a WMS in UAE
Using WMS systems will not make you wait long for profits. The system allows you to improve the efficiency of your business in the following ways:
Reduced Costs
Using WMS helps you reduce costs by optimizing storage, retrieval, and packing processes.
-
Optimizing storage. A WMS uses advanced algorithms to determine the best locations for storing items, maximizing warehouse space and reducing wasted areas. By organizing inventory in a way that minimizes unused space, businesses can avoid the costs associated with renting additional storage facilities. It also reduces the time staff spends on their tasks and the number of employees needed to handle the same workload. This ensures peak efficiency and reduced labor costs.
-
Retrieval process. WMS lowers costs by streamlining the picking process, guiding workers along optimized paths for faster item location and reduced labor time, in turn reducing labor costs. It minimizes picking errors and boosts order accuracy, cutting costs tied to returns and unhappy customers. WMS software also helps manage perishable inventory by picking items with the shortest shelf life first. This ensures that products are used before they expire, boosting sales and reducing waste. This way businesses can avoid losses from spoiled goods.
-
Packing processes. A WMS can provide detailed packing instructions, ensuring that items are packed correctly. This reduces the likelihood of damaged goods and returns, saving costs associated with re-shipping and handling. Additionally, by automating packing instructions and integrating with transport systems, WMS optimizes package sizing and carrier selection, leading to significant savings on materials and shipping.
A survey by Logistics Management found that warehouses are the most common location for packing and fulfillment activities, with ResearchGate estimating that order picking costs make up 55% of total warehousing expenses.[?]
Improved Inventory Accuracy and Visibility
A WMS enhances inventory accuracy by providing real-time tracking and precise data on the location, quantity, and status of all items within the warehouse. This reduces the likelihood of errors caused by manual data entry, misplaced items, or outdated records. With accurate inventory data, businesses can minimize stock discrepancies, ensuring that inventory counts are always correct and up-to-date.
Enhanced visibility also supports better decision-making, as managers can monitor trends, forecast demand, and plan for future inventory needs more effectively.
Faster Order Fulfillment and Delivery
The filling of goods and their delivery directly depend on how the warehouse is managed. Faster order fulfillment and delivery basically need:
-
Picking routes. There need to be efficient picking routes that minimize the time and effort required to gather items for orders.
-
Quality control. Effective management includes checks to ensure items are packed correctly and securely, reducing the chances of damage during delivery.
-
Carrier coordination. Efficient warehouses communicate effectively with carriers, scheduling pickups and deliveries to ensure timely arrival at the customer’s location.
A WMS helps achieve all of this with ease. The streamlined operations minimize the lag time in order processing, allowing businesses to swiftly move products from warehouse to customer, thus reducing delivery times.
Enhanced coordination between fulfillment activities and delivery systems through the help of WMS ensures the moment an order is completed, the delivery process kicks off immediately. This minimizes the transition period and ensures that customers receive their orders promptly.
Enhanced Customer Satisfaction
Using a WMS can enhance order fulfillment, speed up deliveries, and decrease inaccuracies in packing and dispatching. All these lead to higher customer satisfaction and loyalty, improving your brand reputation.
Additionally, suppliers may benefit from reduced wait times at loading bays and docks, ultimately improving relationships with them.
Key Features of a Modern WMS System
Here are some key WMS features that will improve your inventory workflow.
Inventory Management and Tracking
An inventory tracking system follows inventory through every stage of the supply chain, including ordering, transit, receiving, storage, and order fulfillment. It also includes processes for returns, exchanges, and warranties if necessary.
To give you an idea of how a modern WMS helps you achieve that, we’ll explain using the features of the FirstBit ERP. The FirstBit WMS software has the following abilities that helps manage and track inventory:
-
Stock count management. It tracks inventory from ordering to order fulfillment by keeping track of all the items that your warehouse currently has and placing orders accordingly to prevent overstocking.
-
Minimum/maximum stock levels. The function helps eliminate overstocking or out-of-stock problems by defining every item's minimum and maximum values and getting automatic alerts.
-
Expiry date management. Manage and sell products that come with an expiration date first to mitigate wastage and increase your profit margins.
-
Batch management. Be it auto spare parts, steel items, or heavy-duty machinery, it lets you manage your stock in batch and even process order batches seamlessly.
-
Negative stock management. Enhance the accuracy of the cost of goods sold by avoiding the issue of negative inventory by analyzing the order and shipping dates.
-
Label printing. If you need labels for your inventory, sets, bundles, or inbound or outbound deliveries, you can connect FirstBit software with your label printer.
-
Barcode management. Track products coming in and going out of your warehouse using barcode scanners and PDA devices For example, FirstBit ERP can generate 1D and QR codes for your inventory items.
-
Automated data collection (ADC) using handheld devices. Use handheld devices to scan barcodes and labels to capture stock data across your warehouse automatically.
Order Fulfillment and Shipping
A modern Warehouse Management System (WMS) helps with order fulfillment and shipping by offering several useful features.
- First, it automates order processing, which means it handles the entire process from receiving orders to picking, packing, and shipping them, reducing the need for manual work.
- The system also uses smart picking methods like batch picking (picking multiple orders at once), zone picking (picking from specific areas of the warehouse), and wave picking (picking orders in waves based on priority), which makes finding and picking items faster and more efficient.
- The system integrates with shipping carriers, allowing it to create shipping labels, schedule pickups, and provide tracking information, making the shipping process smoother. It also has packing optimization, which determines the best way to pack items based on their size and weight, ensuring they are packed efficiently and safely. Order accuracy is verified through barcode scanning to make sure the right items are picked and packed.
- Finally, the system uses dynamic slotting to place frequently ordered items in easily accessible locations, and it generates detailed reports and analytics to help improve the order fulfillment and shipping processes continuously.
Warehouse Layout and Space Optimization
Warehouse layout refers to how the space within a facility is arranged to optimize production and distribution flow. A good WMS should help optimize warehouse layout and space efficiency.
FirstBit ERP, for example, offers comprehensive tools to improve warehouse layout. It includes automated slotting, which organizes items based on size, weight, and frequency of use, ensuring that frequently accessed items are easily reachable. This makes the best use of available space and improves efficiency.
It also supports dynamic bin location management, allowing you to create a detailed and hierarchical structure of storage locations within the warehouse. This system ensures that all items are stored in the most optimal locations, making it easier to locate and retrieve them quickly.
Labor Management and Productivity
Labor productivity is one of the key performance indicators for warehouse operations. It measures worker efficiency and resource utilization. One of the most effective methods to boost labor productivity is using your WMS data, which offers valuable insights into processes, workflows, and performance.
Inbound Logistics says many warehouse workers spend about 60% of their time picking orders.
A warehouse management system can help predict labor requirements, generate schedules, minimize travel time within a warehouse, and assign appropriate tasks to employees based on their skill level, proximity, and other relevant factors.
WMS can also enhance employee morale by establishing a more relaxed, organized, and safe working environment where workers perceive that their time is valued and used effectively.
Reporting and Analytics
A WMS is a proper knowledge archive through its diverse reports and analyses. Warehouse management system reports come in a variety of forms, but what makes them so valuable, and how can they change the trajectory of your business?
Here are the examples of reports:
-
Inventory reports. It provides a detailed view of current inventory, including stock levels, pending receipts, and stock thresholds. You may use this data to improve purchasing and sales campaigns, avoid overstocking or stockouts, and predict future stock needs.
-
Product movement analysis. This tracks product turnover rates to reveal fast and slow-moving items. Insights from this data will help you optimize storage, product placement, and purchasing decisions, leading to cost savings and better customer satisfaction.
-
Labor efficiency reports. It assesses workforce productivity, identifying strengths and areas for improvement. By optimizing training and workflows, businesses can enhance productivity and employee satisfaction.
-
Order accuracy reports. These reports highlight the accuracy of the picking, packing, and shipping processes. Identifying frequent errors allows you to reduce costly returns and improve customer satisfaction.
-
Storage space analysis. This optimizes warehouse space use by examining product storage, rotation, and access. Improved layouts lead to faster processing times and lower operational costs.
-
Operational cost reports. The reports provide a view of operational expenses, helping identify cost-saving opportunities through automation, better vendor contracts, and streamlined workflows.
-
Sales trend analysis. By combining sales data with inventory insights, you can forecast market trends and align stock with customer demands, ensuring the availability of popular items.
-
Return reports. These reports analyze reasons behind returns, offering insights to refine product offerings and reduce return rates, enhancing brand loyalty.
-
Safety and compliance reports. Ensuring products are stored and handled according to regulations, these reports minimize legal liabilities and bolster brand reputation.
-
Predictive analysis. Using AI and machine learning, predictive analysis anticipates future challenges like stockouts or equipment failures, helping your business stay agile and prepared.
If you're in search of a warehouse management software that encompasses all the previously mentioned features, then the WMS FirstBit ERP module would be an ideal match for your business needs.
Types of Warehouse Management Systems
The operation of your warehouse management system depends on the type of system you integrate. Each module is unique, each has its own advantages and disadvantages.
Standalone WMS
A standalone Warehouse Management System (WMS) is a specialized software dedicated exclusively to managing warehouse operations. It offers advanced features for inventory tracking, order management, space optimization, and labor management without integrating with other enterprise systems. It is a practical choice for small to medium-sized businesses due to its cost-effectiveness and ease of implementation.
Advantages
-
Specialization in warehouse management
-
Greater flexibility in deployment and integration
-
Scalability for various business sizes and needs
Disadvantages
-
May require complex integration efforts with other business systems leading to potential issues with data consistency and flow.
-
The high degree of customization and specialized features of standalone WMS can result in higher upfront costs, both in terms of the software itself and the need for specialized hardware or infrastructure.
Integrated ERP Modules
The WMS ERP module integrates warehouse management with other ERP solutions, providing data sharing and automation.
This system enhances real-time visibility and data exchange between warehouse management and other functions like inventory, accounting, and finance. It is suitable for middle and large enterprises and offers a comprehensive platform for unified management of warehouse operations and broader business processes.
Advantages
-
Allows for data management across all business functions, ensuring consistency in information from inventory to financials
-
Facilitates smooth integration of warehouse data with other business processes, such as procurement and sales, enhancing overall operational efficiency
Disadvantages
-
It may need more specific warehouse management features that standalone systems provide, which could be a drawback for specialized needs
-
The setup process can be complex and time-consuming, requiring significant resources
-
The initial investment and ongoing maintenance can be substantial, possibly not justifiable for smaller businesses with simpler operations
Cloud-Based WMS
A cloud-based warehouse management system is a software hosted on remote servers and accessed over the internet, designed to optimize and automate the operations of a warehouse. The solution provides higher security measures, including encryption and regular audits, making it often more secure than on-premises systems.
A cloud-based WMS offers scalable, flexible, and optimized warehouse management for businesses of all sizes. It also designed to handle connectivity issues with features like local caching and data synchronization.
Advantages
-
Lower deployment and operational costs, with businesses only paying for what they use
-
Accessibility from anywhere with internet access, making it easier to manage multiple warehouse sites and scale as business needs change
-
Enhanced security measures, like encryption and audits, make it more secure than on-site systems
-
Designed to address connectivity issues through local caching and data synchronization
Disadvantages
-
Requires reliable internet connectivity, which can be a challenge for some businesses
-
Despite high security, online systems are always at risk of data breaches
-
As businesses grow and require more resources, costs can rise
-
It may need help integrating with existing on-premise systems
Supply-Chain Execution Modules
The supply chain module is a system designed to improve supply chain processes and warehouse operations. It works well for companies with complex supply chain needs. This WMS type can easily work with other supply chain software, providing businesses with a complete solution for managing warehouses effectively as part of the overall supply chain system.
Advantages
-
Can integrate with other supply chain software
-
Enhance inventory management efficiency
-
Increase the accuracy and speed of order fulfillment
-
Simplify and expedite shipping procedures
-
Boost customer satisfaction and decrease operational costs significantly
Disadvantages
-
May necessitate extensive customization and integration with other systems
-
May lead to higher costs and a steeper learning curve for users
ERP and WMS: Understanding the Relationship
ERP systems and WMS have different, but sometimes overlapping, roles within a company. They are distinct in what they aim to do, what features they offer, how widely they are used, and which of the business they handle. Knowing these differences can help companies choose the right system to match what they need for operations.
ERPs provide a wide range of valuable functionalities, including a warehouse management module, that can be applied across an entire company and adaptable for use in various industries. In contrast, standalone WMS software offers specialized solutions designed to optimize warehouse and manufacturing processes.
WMS systems have more detailed, industry-specific features that can be customized to fit an organization's workflow. You should analyze your project's needs to decide if you only need a WMS or if additional functionality is also important.
How ERP and WMS Systems Integrate for Maximum Value
Improving communication between two systems is a good strategic move. The interaction between these systems is necessary to ensure optimal performance. Each system depends on data from the other to effectively manage warehouse operations and make well-informed business decisions.
-
Making sure everything runs smoothly is important for businesses. Connecting WMS and ERP systems helps different departments work well together. This leads to better efficiency and productivity.
-
Combining systems gives you up-to-date information on your inventory. This helps you keep track of where products are and make smart decisions quickly.
-
Integrating systems can be tricky. Common problems include differences in data and compatibility issues. Recognizing and dealing with challenges is the first step to fixing them.
-
Addressing integration challenges there are solutions available. Providing training, keeping data consistent, and regularly checking systems can help businesses integrate smoothly and efficiently.
WMS FirstBit ERP Module
All the most necessary features for warehouse management are integrated in the WMS FirstBit module, among them:
-
Monitoring of all available warehouses
-
Bin locations management
-
Storage of documentation in one place
Here is the list of all the warehouses you have. These warehouses can belong to different projects if you are running more than one business. Create new warehouses, customize the specific information (responsibility, financial documents type) and manage them in one click.
Keep all applications in one place for your convenience. In WMS FirstBit ERP, your applications with all detailed information will be in one tab. You can also keep track of their status and required date, allowing you to manage your time more efficiently.
Warehouses often organize their space into zones like storage areas, sections, and individual shelves or bins to reduce mistakes and make it easier to find and pick items for shipping or other needs. When products arrive, they're given a unique bin location code that marks exactly where they're stored.
In WMS FirstBit ERP, if your warehouse is organized this way, you can use the Bin Locations feature. This tool lets you create a clear layout of your storage spaces, assign incoming products to specific spots, and quickly locate them when it's time to or use them.
You can define a hierarchic (multiple-level) structure of the warehouse with storage areas divided into sections, each with rooms, each room with rows of multi-level racks, shelves, and cells (or bins) or any other structure levels fitting your business.
Among other things, the WMS module in the FirstBit ERP meets all the requirements of modern WMS software, such as warehouse management software, including inventory tracking, order fulfillment, shipping, and real-time tracking. It also offers analytics to streamline warehouse operations.
F.A.Q.
1. How can a WMS help with inventory accuracy challenges?
2. What role does WMS play in addressing fluctuating demand?
3. Can WMS tackle the issue of warehouse space optimization?
4. How does a WMS improve order processing times during peak periods?

Anna Fischer
Construction Content Writer
Related terms
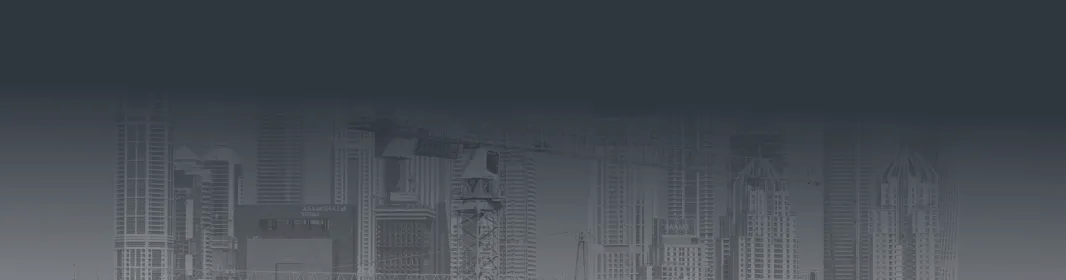
See FirstBit ERP solutions in action
Discover how our system solves the unique challenges of contractors in a personalized demo.
After the demo you will get a quotation for your company.
After the demo you will get a quotation for your company.