Every contractor knows the feeling: You're reviewing project drawings when you spot a discrepancy that could derail your timeline. The structural plans show one beam depth, while the architectural drawings show another. Your crew is waiting, and every hour of delay costs money.
Project delays and miscommunication on construction sites often stem from unclear specifications and information gaps. When questions arise about drawings, specifications, or site conditions, construction teams need a formal, trackable way to get answers before these uncertainties become costly issues.
This is where RFIs (Requests for Information) play a crucial role in construction project management, serving as the standard method for documenting and resolving technical questions. This guide will help you streamline your RFI process, showing you practical strategies to write effective requests and reduce response times.
What is an RFI?
An RFI (Request for Information) in construction is a formal written document used to obtain essential project information, clarify ambiguities, or resolve discrepancies in construction documents. When contractors, subcontractors, or other project stakeholders encounter unclear specifications, conflicting information, or need additional details, they submit an RFI to get clear, documented answers before proceeding with work.
Let's look at a simple example:
Imagine you're reviewing construction drawings for a commercial building renovation project. You notice several technical specifications that require clarification: The structural drawings show a beam connection detail, but the specification for the bolt grade and torque requirements is missing.
Instead of making assumptions you create an official request (RFI) where you clearly describe what's unclear and send it to the architect, designer or engineer for clarification. It will be very useful to attach relevant photos or drawings showing the problem area.
For example: Drawing A-101 shows an interior wall between the kitchen and living room. Please specify:
- Required wall thickness
- Material type
- Sound insulation requirements
This information is urgently needed for material ordering.
Why are RFIs Important in Construction?
-
Clarifying specifications and drawings. For example, when an electrical contractor notices that the power requirements for HVAC equipment don't match between mechanical and electrical drawings, an RFI helps resolve this discrepancy before installation begins. This prevents costly rework and ensures proper system functionality.
-
Preventing delays and cost overruns. Research by the Construction Industry Institute shows that inadequate specifications and delayed RFI responses account for approximately 22% of construction cost overruns. In one notable legal case, a single unclear RFI response from the Army Corps of Engineers resulted in a $1.3 million award in direct damages, plus significant interest costs spanning nearly four years.[?]
-
Serving as legal documentation. RFIs create a paper trail of decisions and changes. For instance, if questions arise about why certain materials were used or methods were followed, properly documented RFIs provide legal protection by showing that decisions were approved by appropriate parties.
-
Enhancing communication and collaboration. They facilitate clear communication between all project stakeholders. When a question about specifications arises, the RFI process ensures architects, contractors, and suppliers are all working with the same information.
In construction procurement, three essential documents serve distinct purposes in gathering information, requesting pricing, and soliciting solutions. Each plays a crucial role at different project stages.
The request for information helps you plan a new sustainable building project, you might send RFIs to contractors to learn about different technologies and methods. This initial exploration helps shape your project's direction.
The request for quotation comes into play when you know exactly what you need. RFQs focus on price comparison for specific, well-defined items or services. If your project requires particular materials, an RFQ helps you find the best price from qualified suppliers – like getting multiple quotes for the exact same product.
The request for proposal is more like inviting potential partners to present their vision for solving a complex challenge. When building a specialized facility, you need more than just a price quote – you need to understand contractors' approaches, experience, and problem-solving capabilities. RFPs allow you to evaluate the complete package of expertise and innovation they offer.
These tools often work together throughout a project's lifecycle. Starting with RFIs to understand solutions, moving to RFPs for comprehensive proposals, and using RFQs for specific materials creates a systematic approach that builds a solid foundation for successful project execution.
The RFI Process Explained
1. Identifying the Issue
Construction professionals must recognize when an issue warrants a formal RFI. Not every question requires this level of documentation, but certain situations demand it. RFIs are necessary when:
-
Encountering design discrepancies that could affect construction quality or safety
-
Seeking clarification on technical specifications or material requirements
-
Requesting additional information about site conditions or existing structures
-
Addressing conflicts between different design disciplines (architectural, structural, MEP)
-
Proposing alternative solutions or value engineering options
-
Documenting changes in field conditions that differ from contract documents
-
Clarifying contract terms, project schedules, or procedural requirements
For instance, mechanical drawings showing ductwork running through a structural beam is a classic interference conflict between different building systems. If mechanical drawings show ductwork running through a structural beam, this conflict requires an RFI to determine whether the ductwork needs to be rerouted or if the structural engineer can approve a beam penetration.
Similarly, when specifications are unclear about material requirements or installation methods, an RFI helps prevent costly mistakes. The key is to identify issues that could impact project timeline, budget, or quality before they become problems.
2. Drafting the RFI
Creating an effective RFI requires clarity and precision. Begin with basic project information, including the project name, date, and RFI number. The heart of the RFI should clearly state the problem, referencing specific drawings or specifications involved.
For example, rather than writing "Need clarification about wall height," specify "Drawing A-201 shows conflicting wall heights of 10' and 12' between grid lines B and C."
Include relevant photos or sketches to illustrate the issue. If possible, propose potential solutions to demonstrate you've thought through the problem. Always specify when you need the response based on the project schedule.
3. Submitting the RFI
The submission process must follow established project protocols. Most modern construction projects use specialized software for RFI submissions, ensuring proper routing and tracking.
Submit the RFI to the designated recipient, typically the architect or general contractor, and copy other stakeholders who need to be aware of the issue.
You can make it through the project's designated channel – whether it's construction management software (like FirstBit ERP), project web portals, email, or hardcopy forms – as specified in your contract documents.
Proper submission timing is crucial — don't wait until the last minute when an issue could affect critical path activities. Keep track of your submission in an RFI log and set up a system to follow up if responses are delayed.
4. Reviewing and Responding to the RFI
The review process often involves multiple parties, including designers, engineers, and contractors. Each participant should evaluate the proposed solution from their perspective, considering how it might affect their scope of work.
Responses should be clear, complete, and actionable. Technical language should be precise but understandable. If the response generates new questions or concerns, address them promptly through follow-up communication.
5. Implementing the Response
Once you receive an RFI response, swift and accurate implementation is crucial. Share the information with all affected team members, ensuring everyone understands the direction provided. Update relevant project documents to reflect any changes specified in the response.
If the resolution affects the project schedule or budget, document these impacts and adjust project planning accordingly. Clear communication during implementation helps prevent misunderstandings and ensures the solution is executed correctly.
6. Closing the RFI
The RFI process isn't complete until proper closure is documented. Verify that the response fully addresses the original question and that all parties understand and accept the solution. Ensure any required changes are incorporated into project documents and that the implementation meets the specified requirements.
Document the closure in your RFI tracking system, including the date and any notable outcomes. This documentation becomes valuable for project records and can help inform future decision-making processes.
How to Create an RFI in Construction
A well-prepared RFI saves time, prevents misunderstandings, and helps maintain project momentum. Here's how to prepare a professional RFI that gets results:
-
Use a standard template. Start with your company's or project's approved RFI template. Most construction projects have standardized forms to ensure consistency across all communications. If no template exists, create one that includes all essential sections: header information, question area, response section, and signature blocks. Using a consistent format helps recipients quickly locate information and process requests more efficiently.
-
Include project information. Begin your RFI with complete project details. This includes the project name, contract number, location, and date of submission. Add your RFI tracking number, which typically follows a predetermined sequence (e.g., RFI-001, RFI-002). Also include your contact information and role in the project, making it easy for respondents to reach you if they need clarification.
-
Write a clear subject line. The subject line should immediately convey the topic of your inquiry. Instead of vague descriptions like "Window Question," use specific subjects such as "Exterior Window Frame Finish Specification - North Elevation." A precise subject line helps recipients prioritize responses and allows for easier document tracking throughout the project.
-
Provide specific references to drawings or specifications. Always reference relevant project documents in your RFI. Include drawing numbers, specification sections, and page numbers. For example, write "Refer to Drawing A-301, Detail 5, and Specification Section 08520, Page 3, Paragraph 2.3." These specific references enable reviewers to quickly locate the information in question and provide accurate responses.
-
Explain the issue concisely. Present your question or concern clearly and briefly. Avoid lengthy explanations that might confuse the issue. State the problem, its location, and why clarification is needed. For example: "The window schedule shows conflicting frame depths between typical details and manufacturer specifications. Please confirm required frame depth for Type W1 windows."
-
Attach relevant photos or sketches. Visual aids significantly improve understanding of the issue. Include photographs of the area in question, marked-up drawing excerpts, or simple sketches that illustrate your concern. Make sure images are clear and properly labeled. Use arrows or highlights to draw attention to specific areas requiring clarification.
-
Suggest potential solutions. When appropriate, propose possible solutions to the issue. This demonstrates your proactive approach and can expedite the response process. Present your suggestions professionally, acknowledging that the final decision rests with the design team. For example: "We suggest using the manufacturer's standard 4-inch frame depth to maintain consistency with other window types on the project."
-
Specify required response date. Clearly indicate when you need the response to maintain the project schedule. Be realistic with your timing requirements, considering the complexity of the question and the review process. Include any critical dates or milestones that might be affected by the response. For instance: "Response required by [date] to maintain window fabrication schedule and avoid delivery delays."
Common Challenges with RFIs
Poorly written RFIs can seriously harm a construction project. This is all about money and time.
The financial impact of RFIs on construction projects is significant. Each RFI response costs construction firms approximately $1,080, with the total project impact potentially reaching $859,000. These substantial costs highlight the importance of efficient RFI management and the need to minimize unnecessary requests through proper planning and documentation.[?]
1. Additional Costs
Additional costs present a significant challenge in the RFI process. Each RFI carries hidden expenses beyond just the administrative time spent creating and processing it.
When RFIs face delays or require multiple revisions, they can trigger chain reactions of schedule impacts and labor standby costs. Even seemingly simple RFIs can become costly when they affect multiple trades or require extensive coordination.
These expenses are often overlooked in initial project budgets but can accumulate significantly, especially on complex projects with hundreds of RFIs.
Consider a case where ductwork conflicts with a structural beam: While the initial RFI submission might take just a few hours to prepare, the resulting costs can multiply rapidly.
The project team must halt mechanical installation (causing crew standby costs), coordinate multiple design revisions (requiring additional engineering fees), possibly modify prefabricated materials, and adjust the schedule of dependent tasks.
What started as a simple RFI could easily accumulate substantial unexpected costs through direct expenses and indirect impacts on project timeline and resource allocation.
2. Delayed Responses
Delayed responses to RFIs create a domino effect on project progress. When responses are slow or incomplete, teams must submit follow-up requests, forcing work stoppages and disrupting planned sequences. This causes a ripple effect where multiple trades face delays, equipment sits idle, and scheduled activities fall behind.
3. Unclear or Incomplete Information
The precision and completeness of RFI submissions directly determine the quality of responses received. Vague or partial information in initial requests inevitably leads to inadequate solutions that fail to address the core issue.
Without specific technical details, site conditions, and relevant constraints, respondents cannot provide accurate, implementable solutions. This information gap creates a cycle of clarifications and revisions that could have been avoided with a comprehensive initial submission.
The resulting delays affect not only the specific task in question but also impact the overall project schedule and coordination efforts.
4. Lack of Coordination
Fragmented communication and isolated decision-making create major problems in RFI management. When teams work separately on connected systems, they often submit multiple RFIs about the same issues. This creates extra work for project managers, slows down response times, and often leads to different solutions for the same problem. Teams then receive conflicting instructions for connected work, causing confusion and mistakes during construction.
Without a central system to manage RFIs, these problems get worse as no one can track which questions have already been asked and answered.
5. Unjustifiable RFIs
Unjustifiable RFIs represent a concerning challenge in construction project management. Studies show that approximately 13.2% of total RFIs submitted are considered "not justifiable," creating unnecessary administrative burdens and project costs.[?]
These frivolous requests often include information already available in contract documents, questions that could be answered through basic document review, or queries aimed at building potential claim documentation rather than seeking genuine clarification.
Some contractors may strategically use unjustifiable RFIs as a tool to build future claims, suggesting the project was inadequately designed at bid time. By generating large volumes of RFIs, they create a paper trail that could influence legal proceedings, where the sheer number of RFIs might be presented as evidence of design deficiencies or project mismanagement.
Best Practices for Managing RFIs in Construction
Try these practices to make your RFIs management smooth and successful.
-
Standardize the RFI format. A standardized RFI format ensures consistent and efficient communication across all project stakeholders. Your template should include clearly defined sections for project details, issue descriptions, and proposed solutions. Implement a structured numbering system that identifies specific trades or building systems – for example, "MEP-001" for mechanical issues or "STR-002" for structural concerns. Each RFI should contain essential elements, including project name, submission date, required response date, and detailed reference documentation.
-
Set clear deadlines for responses. Effective deadline management is crucial for maintaining project momentum. Establish response timeframes based on the RFI's impact on the project schedule and its technical complexity.
Critical issues affecting project progress require quick turnaround times, typically within 48 hours, while standard queries can allow 3-5 business days for response. When setting deadlines, consider the complexity of the issue and the number of parties needed for review. Include these deadlines prominently in the RFI submission and establish a follow-up protocol for overdue responses.
-
Be clear and specific in your RFI. Precise communication in RFIs prevents misunderstandings and reduces follow-up questions. Each submission should include specific details about the location, scope, and nature of the issue. Instead of general questions, provide exact references to drawings, specifications, or building locations.
For example, specify "Requesting clarification on the connection details between steel beam B1 and column C4 on Level 3, drawing S-301." Include relevant photographs or marked-up drawings to illustrate the issue clearly. When appropriate, present potential solutions with supporting rationale.
-
Track RFIs for accountability. Maintain a centralized log that records submission dates, due dates, current status, and final resolutions. Construction management software can automate this process, providing real-time updates and generating performance metrics such as average response times and common issue types.
Regular review of tracking data helps identify process bottlenecks and recurring issues that may require broader project attention. This systematic documentation creates a valuable record for project management, serves as a reference for similar future situations, and provides essential documentation for potential dispute resolution.
How FirstBit ERP Simplifies RFI Management in Construction
ERP systems provide a central repository for all RFIs, eliminating the need for scattered emails, spreadsheets, and paper documents. FirstBit ERP is a centralized platform that allows all stakeholders to access, review, and respond to RFIs in one place.
Our system will streamline your RFI process through its centralized platform, making submission and tracking simple. Within the system, users can create and submit RFIs without relying on external emails or document management tools. Each RFI automatically receives a unique identification number and timestamp, creating an organized record-keeping system that enables efficient tracking.
FirstBit ERP's automated notification system transforms how stakeholders stay informed throughout the RFI process. The system immediately alerts team members when new RFIs are submitted or their status changes, eliminating the risk of overlooked requests. You, project managers, and engineers each receive customized notifications based on their roles, while automated reminders for approaching deadlines help keep the RFI process moving forward efficiently.
The system's seamless integration with project timelines and schedules provides valuable insights into how RFIs impact project progress. By linking RFIs directly to project milestones, you can instantly see how pending requests affect the critical path and make informed decisions about resource allocation.

Anna Fischer
Construction Content Writer
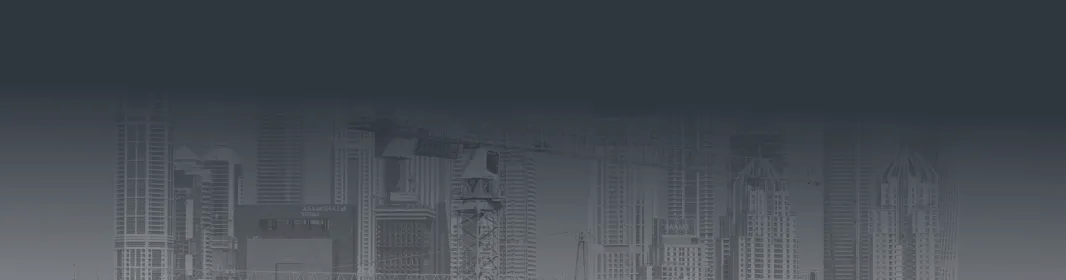
See FirstBit ERP solutions in action
Discover how our system solves the unique challenges of contractors in a personalized demo.
After the demo you will get a quotation for your company.
After the demo you will get a quotation for your company.