Construction costs in Dubai are more complex and present more challenges in 2025 than ever before. Global supply chain issues that started during the COVID-19 pandemic still impact the industry. Fluctuating material costs and delivery delays make it difficult to plan your budget.
If you're here, chances are you are looking for ways to optimize these expenses to prevent or resolve cost overruns and other related issues during a construction project. You may need more information about strategies that will work for your business or learn how to resolve cost-related issues you are already experiencing.
This article will provide practical solutions to optimize construction costs in your construction projects. These solutions include effective budgeting, resource allocation, and software technology.
What Does Cost Optimization Look Like in a Construction Business?
Cost optimization reduces expenses while maintaining or improving a project's quality and efficiency.
It is important to note that learning how to optimize construction costs does not mean simply cutting costs left and right. Effective cost optimization means planning for the unforeseen. It also means using resources where they are most needed and using tools that can help streamline overall operations. For example, software for tracking and monitoring expenses.
Optimization is about achieving more without using or spending more. You should evaluate direct and indirect costs throughout a project's lifecycle. Direct costs that can be optimized include labor, materials, and equipment. Indirect costs include project management, administrative costs, and unexpected delays. They also include everyday construction costs, such as senior staff salaries, office building rent, stationery, utilities, and office furniture.
Optimization strategies for both will keep your bottom line up and your business competitive.
Cost Optimization in Action
Consider this: A mid-sized company is in the process of building a new commercial office building as part of construction in Dubai. While planning the project, the project manager and other stakeholders decided on traditional materials like concrete and steel. Their reasoning is that these materials are more expensive but are also very strong and durable – perfect for the building project.
However, as the project progresses, the project manager reevaluates this decision. He researches alternative materials and discovers that modern prefabricated materials could be used instead of concrete and steel. He also learns that these prefabricated materials are both cheaper and can speed up the construction process by at least 15% per phase.
The time savings are due to the off-site construction of the prefabricated components. Plus, there is a reduced need for on-site labor to pour or shape traditional materials. Many prefabricated materials are also standardized, so they are produced in bulk. This process is much faster than creating custom materials.
Thus, the project manager has saved time and money during the project. Most importantly, his new decision has not reduced the quality of the construction. Prefabricated material, when designed to meet load requirements and building codes, meets industry standards for strength and durability.
Prevent cost overruns
Register expenses in FirstBit ERP
Request a demo
The Importance of Cost Optimization in Construction
Reducing construction costs can mean the difference between project success or failure.
Apart from that, here are some of the other reasons cost optimization is essential.
1. Helps Stay On-Target and On-Budget
Unfortunately, too many construction companies have a reputation for project and cost overruns. This usually happens because of mismanagement, unexpected delays, and material price increases.
Cost optimization strategies can help project managers make more accurate forecasts. This will help them deal with extra expenses and allocate their existing resources more effectively. Being in better control of a project minimizes overspending while improving profitability.
2. Reduces Waste
Cost optimization strategies can help project managers make more accurate forecasts. This will help them deal with extra expenses and allocate their existing resources more effectively. Being in better control of a project minimizes overspending while improving profitability.
Excess building materials and inefficient processes result in too much waste on construction sites. Cost optimization can help identify and reduce these inefficiencies. For instance, tracking material usage can prevent over-ordering.
Builders often order more supplies than they need or may not efficiently use the material they ordered. This leads to unused materials lying around or, worse, scrap lying around.
Cost optimization strategies, such as tracking material usage, allow builders to keep track of how much material is needed and being used. If there is a consistent pattern of surplus materials, they can adjust future orders. This is instrumental in reducing waste and not using more of the budget than is necessary.
The best part of reducing waste is that your business will improve its sustainability efforts.
3. Builds Trust and Reputation
Clients and other stakeholders want to work with construction companies they can trust. You can build trust in the construction industry by using cost-optimization strategies to meet all your financial commitments.
For instance, you should provide clients with a transparent budget that reflects accurate construction costs for material, labor, and anticipated risks. This way, clients know what they are paying for.
Moreover, you must keep your clients informed about all budget changes because of unexpected issues. Regular updates assure clients that your company is managing their budget effectively.
This type of reliability drives reputation, which is critical in an industry where referrals and repeat business are essential to growth.
4. Enhances Teamwork
Cost optimization can also help you create a collaborative work environment in your office. When your employees know the project goals, timelines, and budgets, they can work together better to ensure a successful project.
5. Improves Safety
Cost optimization includes investing in safety protocols, training, and equipment that help prevent accidents on-site. When you know where and how to allocate your workers, you create a safer project site without unnecessarily increasing construction costs. Your workers are protected, and so is your business from losing money due to lawsuits and downtime.
6. Strengthens Client Relationships
Your clients want transparency and reliability from you, especially regarding budgets and timelines. Optimizing construction costs enables you to provide your clients with clear and accurate financial estimates and regular budget updates throughout the project.
When your clients see that you efficiently manage all the necessary resources and, most importantly, stay within budget, they are more likely to use your company for future projects.
7. Ensures Timely Deliveries
Construction delays can spell doom for a project's budget and your company's reputation.
By using proactive cost optimization strategies, you can identify smaller issues before they derail the entire project, thanks to the help of the right software.
For instance, project management software provides real-time updates on project progress, including material usage and labor hours, both of which impact construction costs in Dubai.
For instance, project management software provides real-time updates on project progress, including material usage and labor hours, both of which impact construction costs in Dubai.
This visibility will allow you to spot potential delays immediately. You can then reassess the material needs and labor requirements and adjust where necessary to prevent bottlenecks.
If you do not use project management software yet, frequent team meetings can also help prevent costly delays.
8. Supports Long-Term Success
The point of using cost optimization strategies is not solely to get through each project. You should be using cost optimization to build a foundation for the success of your construction business.
Companies that consistently optimize and track construction costs can take on larger projects and be more competitive in a tough market, especially when factoring in construction costs in Dubai for bidding accuracy.
Practical Tips to Improve Cost Optimization in Construction Projects
Cost optimization can only be effective if done proactively. You must focus on the planning and execution stages of your project. Here are practical tips on how to do this.
1. Centralize Data
You should consolidate project data into a single online system. This is a good way to visualize your project spending. Centralized data should include budgets, material orders, schedules, and labor costs.
An overview like this also reduces the risk of errors, oversights, or duplications. Furthermore, readily available data on one platform makes communicating easier for your business' departments.
2. Collaborate Early
Everyone involved, including you as the project manager, architects, engineers, and contractors, should collaborate from the start. This is the easiest way to prevent errors and misunderstandings that could inflate construction costs.
Discussing the project's planning and execution upfront can highlight potential bottlenecks and budget concerns. It gives everyone a chance to agree on solutions before the project starts.
3. Reduce Wastage
Wastage can quickly drive up construction costs. Whether it is excess materials that are never used or mismanaged labor time, it will cost your business a lot of money.
Reduce wastage by adopting the rest of the lean construction principles.
-
Identify the value a customer wants to see from the project. You must understand the needs and expectations of your client. If you do, you can ensure the project delivers what the client values, be it cost savings, quality, or sustainability.
-
Find the value stream (processes that deliver value). Map out the processes that are supposed to complete the project. Identify which activities contribute to the final value of the project. This is the easiest way to eliminate or streamline processes that are inefficient or too costly.
-
Create an uninterrupted workflow. Coordinate tasks and resources so there are no pauses or gaps in the workflow. For instance, workers should be assigned tasks at all times to prevent the project from stalling.
-
Ensure the workflow is based on downstream demand. Communicate with subcontractors and suppliers about what the project needs, whether it is work that must be done or material that must be delivered. Constant communication ensures that resources are available when needed.
-
Always improve processes and workflows where necessary. Work towards continuous improvement by encouraging all project teams to assess and refine their processes. When they find inefficiencies, they can correct them before they affect the project.
These principles will also help you emphasize a project's value while staying efficient. To do this properly, you must learn how to do accurate forecasting and material planning. Software tools can help with this, especially regarding idle labor.
4. Build Strong Supplier Relationships
Construction cost optimization also relies on securing the best pricing for materials and on-time deliveries. This can only happen if your company has long-term partnerships with reliable suppliers. Strong relationships can also mean first access to new building materials and technologies to help your business save money.
5. Choose Energy and Cost-Efficient Materials
Sustainable construction practices are increasingly being demanded for new building projects. Although you may need to pay more for energy-efficient materials, they can provide long-term maintenance and energy consumption savings.
Sustainable choices will allow you to cut operational costs while making your services more attractive to environmentally conscious clients.
6. Encourage Transparency and Accountability
Reducing construction costs and optimizing your budget can only happen if your company culture is one of transparency and accountability. All teams must communicate about budgets, timelines, and resource allocations.
Regular reports and open access to project data will keep everyone informed and facilitate better decision-making for the project, particularly when managing construction costs in Dubai.
Regular reports and open access to project data will keep everyone informed and facilitate better decision-making for the project, particularly when managing construction costs in Dubai.
7. Use Integrated Software Solutions
An integrated software program is one of the best ways to streamline project management within your business. FirstBit ERP, for instance, offers project costing software that helps plan, estimate, and manage construction costs. The software program gives you complete control over every aspect of your project expenses and also helps improve interdepartmental communication.
This software suits all types of construction businesses, contractors, manufacturers, fabricators, and civil engineers, whether the project is valued at thousands or millions of AED.
This software suits all types of construction businesses, contractors, manufacturers, fabricators, and civil engineers, whether the project is valued at thousands or millions of AED.
8. Avoid Making Changes After Construction Starts
Before construction starts, you must complete your planning, design, and project scope. If you make changes afterward, including ordering new materials and reallocating workers, it will disrupt the entire project and cost more money.
For example, a client may decide to change the layout of the building after construction has already begun. This means the project manager will have to order additional or new materials and reallocate labor to make these layout changes.
This delays the timeline because the material must be sourced, paid for, and delivered. The project manager will also have to revise the payment for extra labor hours. This will often require additional estimating to determine the updated budget impact.
9. Encourage Stakeholder Involvement
You must keep all stakeholders in the loop throughout the project's lifecycle. Stakeholders must be regularly informed of all developments and be able to make decisions.
When stakeholders are well informed, it helps optimize costs because it prevents delays and costly rework. This also makes it easier for them to understand limitations and work with you to solve possible further issues.
10. Reward Team Efforts
Your team will work the hardest throughout the project. Remember to incentivize efforts by rewarding them for meeting budget goals and completing tasks ahead of schedule. When your team feels appreciated, they will continue to work towards reducing costs and contribute to the project's success.
Automate all financial operations within one ERP software
Request a demo
Key Challenges in Cost Optimization and How to Overcome Them
Following the above strategies does not mean there will never be any challenges. Some of the most common cost optimization challenges include the following:
1. Dealing With Initial Misalignment
At the start of a project, everyone may not be on the same page. When expectations are misaligned, costs can skyrocket or overrun the budget. This mainly happens when stakeholders do not agree about the project scope or budget.
Pre-construction meetings can help prevent this problem. Everyone should agree on the project's fundamentals beforehand so your company can prevent any form of misalignment.
2. Handling Poor Coordination Between Trades
When the different trades involved in the project do not coordinate well, it can lead to rework, delays, and safety hazards. This can all result in a budget overspend.
Prevent this by implementing a real-time scheduling and communication platform that everyone can access. This will keep each trade aware of the other's progress and open communication channels.
3. Managing Disorganized Documentation
Missing invoices, inaccurate building plans, or outdated blueprints will lead to delays and increased construction costs. Inaccurate or missing information needs to be clarified, and the process of correcting or finding documents causes delays. Missing invoices can stall payments and supply procurement. Inaccurate plans lead to wasted material and expensive extra labor hours.
Using ERP software like FirstBit ERP gives you a consolidated platform to save project information and documents. This gives everyone access to accurate data and ensures informed decisions.
4. Navigating Change Management Issues
Unexpected client requests and unforeseen site conditions can quickly increase construction costs. If you do not implement change management processes before construction starts, your project will suffer delays and budget overruns. Change management refers to handling alterations to the project’s scope or timeline systematically. It ensures all changes are assessed, approved, and communicated.
To implement change management, you must establish clear procedures on how to submit, evaluate, and approve project changes. Define the roles and responsibilities of everyone involved in the change process. Document and communicate all changes to stakeholders. Finally, monitor and control the impact of these changes on the timeline and budget.
As mentioned above, collaborating early on reduces the risk of late-stage changes. Also, ensure that change order procedures are defined and communicated to everyone.
Clear documentation is the best way to define change order procedures. You must also set up approval workflows since the changes must be approved by project managers, architects, and financial personnel. (These steps must also be included in the project contract).
5. Managing Upfront Costs and Resistance
New technologies and redefined efficient processes can help you better manage upfront costs. Resisting investments in new technologies could hamper your efforts to achieve long-term savings, especially when considering construction costs in Dubai.
Certain programs and processes will cost more initially but will save your company money throughout a project's lifecycle. For instance, cost optimization tools and software help improve productivity and reduce waste, saving money.
Software automates processes like scheduling, procurement, and cost tracking. This ensures that resources like labor, equipment, and materials are always allocated efficiently.
Automated procurement helps prevent over-ordering materials and delays due to shortages. These systems also enable real-time budget monitoring, alerting project managers to cost overruns.
Taking human errors out of the process and reducing redundancies lessens the cost of labor and reduces material waste. This leads to fewer delays and better decision-making, which benefits the project and stakeholders throughout the project’s lifecycle.
6. Adapting to Cultural Shifts in the Workplace
Adapting to new technologies and processes means a cultural shift for most construction companies. You will likely experience resistance from your employees and subcontractors who want to continue working in the old way.
The only way to overcome this is to involve everyone in decision-making. You must also offer ongoing training and development to help staff and contractors adapt to new tools and processes.
Real-World Examples of Cost Optimization in Construction
Several well-known construction companies use cost optimization to ensure the success of their projects.
-
PCL Construction emphasizes the importance of early planning and risk management before breaking ground. They use advanced software and analytics to identify cost-saving opportunities and implement risk mitigation.
The company’s preconstruction experts follow best practices to ensure construction efficiency. They also drive value engineering to ensure the best value for the lowest cost for all clients. Yet, the focus is on achieving true value for money, not just cutting costs.
This allows them to deliver projects on time, every time, and within budget, even during challenging market conditions. -
Skanska is another well-known construction company that strongly emphasizes sustainability. The company aims to be carbon neutral by 2045 and uses BIM technology and prefabrication to reduce waste and improve efficiency.
The company is redefining prefabrication standards and practices with each new project. It uses the most innovative technologies, including BIM, material and asset tracking, and just-in-time deliveries.
This allows the company to save money while improving project timelines and building a stronger, positive environmental footprint. It also reduces construction waste and improves worker safety.
Manage your cash flow with confidence
Request a demo
How FirstBit ERP Can Help Optimize Costs for Your Construction Business
If you want to grow your construction business, you need an ERP system even during difficult economic times. Your company needs the technological advances that these systems provide to be truly competitive.
FirstBit ERP makes it easier for your teams to collaborate on projects. The software provides a centralized data platform, ensuring everyone has access to updated data at all times.
You can customize the FirstBit ERP system to fit your specific construction needs. The system considers the size of projects, milestones, and budget. Managing your project through an ERP program means a lesser risk of disruptions that cost more money. It also helps streamline all tasks so your team can complete projects within the set timeline.
Moreover, the FirstBit ERP software solution is flexible and scalable, accommodating your business's expansion over time.
Effective Cost Optimization Is the Tipping Point for Your Construction Business
When you focus on cost optimization, you automatically enhance a project's efficiency. Optimizing costs can see your business through as material costs rise and labor shortages continue in 2024. Modern software like FirstBit ERP can make all the difference by allowing you to take control of each project. You will eliminate inefficiencies, improve collaboration, and make the best decisions for each project while keeping all stakeholders informed.
By optimizing costs today and using the best that technology offers, your company will sustainably grow into future success.
Always know where your money is going
Monitor cash flow in FirstBit ERP
Request a demo
FAQ
1. What is the cost of construction per sq ft in Dubai?
2. What is the cost control method in construction?
3. What are the cost control measures?
4. What is the cost planning process in construction?
5. How to track construction costs?
6. How to develop a cost plan?
7. What is cost based optimization?
8. How can construction projects reduce costs?

Cedric Jackson
Contributing Author
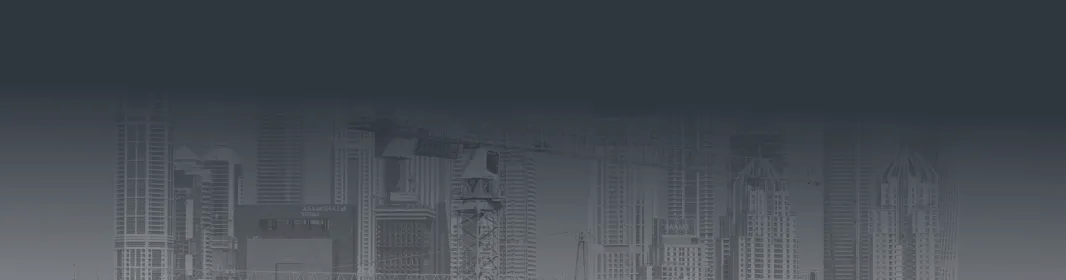
See FirstBit ERP solutions in action
Discover how our system solves the unique challenges of contractors in a personalized demo.
After the demo you will get a quotation for your company.
After the demo you will get a quotation for your company.