Cost overruns in construction have been a persistent issue for the past 70 years, lacking effective control or solutions. Studies have shown that construction projects experience an average of 28% cost overrun. [?]
That statistic represents billions in lost profits, countless strained relationships, and immense stress for everyone involved in construction projects worldwide.
If you're managing construction projects, you know these numbers aren't just abstract figures. They translate into real-world headaches: that unexpected foundation issue that blew your contingency budget, the material price spike you couldn't have predicted, or the scope creep that slowly eroded your profit margin. These challenges affect everyone, from small contractors to major construction firms, and they've become so common that many consider them an unavoidable part of the business.
But here's what years in the industry have taught us: While cost overruns are common, they're not inevitable. Through years of experience and learning from both successes and setbacks, we've identified clear patterns in why projects go over budget and, more importantly, how to prevent it.
In this guide, we'll share practical strategies that have helped real projects stay on track and how you can apply them to your own work.
Understanding Cost Overrun
Cost overruns have consequences that reach beyond just the budget. Understanding cost overruns shows why careful planning, managing risks, and being flexible are so important for keeping projects on track.
What is Cost Overrun in Construction?
A cost overrun occurs when actual project expenses exceed the planned budget. In construction, this typically means spending more on materials, labor, or equipment than initially estimated. This scenario is common across industries, particularly in construction, manufacturing, and software development, where multiple variables can impact initial cost estimates.
Importance of Managing Costs in Projects
In construction, where profit margins are often tight and competition is high, effective cost management is key to maintaining profitability and business growth. When projects exceed their budgets, it can lead to:
-
Reduced profit margins or financial losses
-
Damaged business relationships
-
Fewer opportunities for future work
-
Potential legal disputes
-
Cash flow problems affecting operations and payments
Strong cost-control practices help prevent these issues and keep projects on track for success. These practices can range from traditional methods like detailed cost sheets and regular financial reviews to modern solutions such as ERP systems that track expenses and labor costs.
For example, FirstBit ERP for construction helps you control material usage in real time, equipment use and maintenance, and prices during the procurement process. Both approaches, when properly implemented, provide clear visibility into project spending and early warning signs of potential overruns.
Common Causes of Project Cost Overruns
Many factors can push a construction project over budget. Understanding these common issues is the first step to preventing them.
1. Inaccurate Estimation and Budgeting
The foundation of project success lies in accurate initial estimates. Problems often start with incomplete design documents or a rushed bidding process. When estimators don't have time to review all details or miss important site conditions, the budget falls short before work even begins. Material cost projections and indirect costs like permits or equipment rentals can also be overlooked during this crucial planning stage.
2. Scope Creep
Changes during construction are one of the most common reasons for cost overruns. Known as scope creep, this happens when project requirements gradually expand beyond the original plan through additional client requests and modifications. These changes, while often small individually, can significantly impact both timeline and budget.
Common causes of scope creep include:
-
Project requirements changing after work begins
-
Clients requesting additional features
-
Hidden conditions requiring extra work
-
Design details needing clarification
-
Communication gaps between stakeholders
To avoid cost overruns from changes during construction, clearly define project requirements upfront and establish a robust change management process. This includes getting client sign-off on the initial scope and having protocols for evaluating and approving any requested changes.
Finally, maintain open communication with all stakeholders to address concerns and clarify design details promptly, minimizing surprises during the project.
3. Lack of Project Management Expertise
Keeping a construction project on track takes a good mix of experience and skill. Things like not using resources wisely, making decisions too slowly, and having a poorly planned schedule can all come from gaps in management. If there isn't enough oversight, small problems can easily become big ones. This can lead to having to redo work, delays, and higher labor costs.
To avoid management related setbacks, prioritize comprehensive training and development for project managers. Foster a culture of clear communication and delegate responsibilities effectively to improve decision-making speed and resource allocation. Implement proven project management methodologies, such as creating detailed schedules and proactively monitoring progress, to catch and address small issues before they escalate.
4. External Factors
Construction projects face many outside influences that can impact costs:
-
Weather delays and natural disasters
-
Material price fluctuations
-
Labor shortages and wage increases
-
Supply chain disruptions
-
Regulatory changes and permit delays
-
Market conditions and economic shifts
These factors may be beyond direct control, but planning will help solve the problem. Watching weather forecasts and tracking vendors’ material prices in the project management software or other digital tools for construction.
For example, in FirstBit ERP for construction, FirstBit ERP helps teams monitor these variables by tracking vendor prices, supply chain status, and market conditions. This gives project managers the data they need to make informed financial decisions and adjust plans accordingly.
Prevent cost overruns
Register expenses in FirstBit ERP
Request a demo
Strategies to Prevent Cost Overruns
Keeping projects within budget in a challenging construction market requires more than just good intentions. The following strategies help teams stay on track and maintain financial control throughout the project lifecycle.
1. Detailed Pre-Project Planning
Success starts before the first shovel hits the ground. To ensure thorough preparation, set up a structured planning phase with specific milestones. Take time to review designs using standardized checklists, schedule site visits with stakeholders during optimal conditions, and create detailed cost estimates.
Build contingency funds into the budget and establish a vendor qualification process to get accurate quotes early - this helps avoid costly surprises later in the project.
2. Project Monitoring and Control
Regular monitoring requires a systematic approach to tracking project performance. To accomplish this, set up weekly cost review meetings where actual expenditures are compared against the budget.
Furthermore, implement a coding system for expenses; this will make it easier to identify where money is being spent.
To enhance project monitoring, you should do these key monitoring activities regularly:
-
Track actual costs against budgeted amounts weekly
-
Set up automated weekly report templates in your project management software
-
Monitor labor productivity and material usage
-
Document all changes and their cost impacts
-
Schedule recurring progress meetings at consistent times that work for all stakeholders
To implement a construction cost coding system, begin by categorizing project expenses into standard divisions like site work, foundations, electrical, and mechanical systems, then assign unique numerical codes to each category. Create a clear guide showing how these codes align with specific construction activities and materials, and share it with all project teams including subcontractors and accounting staff.
Integrate these codes into your construction management software and establish a regular review process to ensure consistent usage across all project documentation and invoicing.
3. Clear Communication Systems
Establish strong communication channels between all parties — owners, designers, subcontractors, and suppliers. Quick responses to questions and concerns help prevent costly delays and misunderstandings. Keep detailed records of all project-related discussions and decisions. Use traditional methods such as emails or modern approaches like collaboration tools like Slack and other team communication software.
Set up standardized templates for different types of communications. For example, you can create a conversation in the messenger (or where is more convenient) and add subtopics with narrow specialists. Establish response time expectations for different priority levels.
Furthermore, you will be able to keep all decisions, such as RFI and RFQ, in one system with a hierarchy structure.
4. Effective Planning and Budgeting
Cost overruns can derail even the most promising projects. Implement strategic planning and leveraging modern tools, project managers can prevent budget escalations and maintain financial control. The key is early detection, proactive management, and using the right technologies to support accurate estimations.
Key digital tools that streamline planning:
-
BIM software for detailed 3D modeling and clash detection
-
Drone surveys for accurate site condition assessment
-
Digital takeoff tools for precise quantity calculations
-
Cloud-based platforms for real-time supplier collaboration
Project teams can enhance their technology adoption by starting with basic modules of estimating software and gradually expanding usage as team confidence grows. Begin by assigning power users who can train others and create standard procedures for daily operations. Regular data review sessions help teams make the most of built-in cost databases and mobile verification tools.
5. Training and Development for Project Managers
Invest in continuous education for project teams. Focus on cost estimation, budget management, and contract administration skills. Regular workshops and mentoring programs help build expertise in financial control.
Skilled labor cost management requires a balanced approach. You need to invest in qualified personnel who can deliver quality work efficiently, while also implementing systems that help monitor and optimize labor expenses. This is where digital solutions prove invaluable.
In the Middle East, where skilled labor shortages remain a persistent challenge, comprehensive training programs serve a dual purpose. They not only improve project management capabilities but also help develop a skilled workforce from within. This internal development approach is particularly valuable given the region's high reliance on expatriate workers and increasing localization requirements.
Furthermore, managing labor costs effectively is crucial for project success in construction. While having skilled workers is essential, equally important is the ability to accurately track and control labor-related expenses.
By investing in training, companies can build a sustainable pipeline of qualified professionals while reducing their dependency on external recruitment. Such practices as regular workshops and mentoring programs help build expertise in financial control, ensuring teams can effectively manage costs throughout the project lifecycle.
6. Specialized Software
Modern construction management platforms have become the backbone of effective cost control. These tools do more than just track numbers — they provide real-time insights, automate routine tasks, and flag potential issues before they escalate. When teams are properly trained in using these systems, they become more efficient and proactive in managing project costs.
Here's how these platforms transform daily operations:
-
Automated cost tracking monitors every transaction against preset budgets, sending instant alerts when spending approaches critical thresholds
-
Smart scheduling tools adjust resource allocation based on real-time progress, preventing costly idle time
-
Built-in approval workflows ensure proper authorization for expenses, eliminating unauthorized spending
-
Integrated document management keeps all contracts, change orders, and invoices organized and easily accessible
-
Mobile capabilities allow field teams to update progress and log expenses instantly, reducing data entry delays
-
Custom dashboards provide stakeholders with role-specific views of financial performance
One of the most effective tools for preventing cost overruns is an ERP system designed specifically for construction. For instance, FirstBit ERP offers an all-in-one solution that helps manage project costs before they get out of hand.
How FirstBit Solves Cost Overruns Issue
Gone are the days of waiting for monthly reports to understand project finances. FirstBit ERP creates a live dashboard of your construction operations, where every transaction, from material purchases to labor costs, is instantly reflected.
Project managers can track expenses against budgets as they happen, spotting trends and addressing issues before they impact the bottom line. When a site supervisor updates material usage or a procurement officer places an order, the system automatically updates financial forecasts and alerts relevant team members.
Construction sites often struggle with material shortages or excess inventory, both of which drive up costs. FirstBit ERP connects your warehouse management with procurement and project planning. The system allows you analyze stock movements and material usage trends to optimize resource planning and reduce surplus.
Keep every project on budget
Request a demo
Frequently Asked Questions About Project Cost Overrun
1. What are the early warning signs of potential cost overruns?
2. What's the ideal contingency percentage for different types of construction projects?
3. How do I handle scope creep without damaging client relationships?
4. Should I include subcontractor delays in my risk management plan?

Anna Fischer
Construction Content Writer
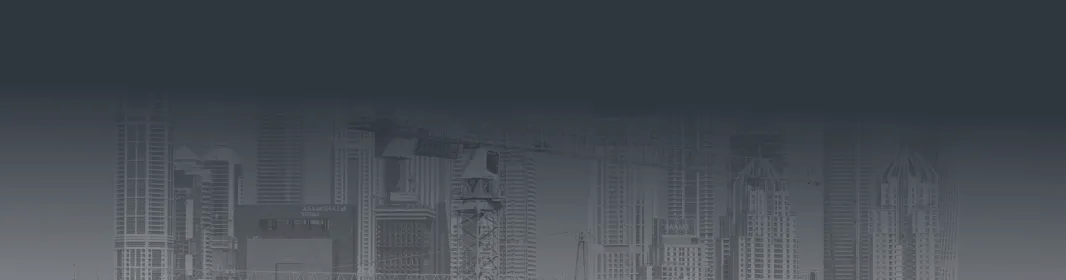
See FirstBit ERP solutions in action
Discover how our system solves the unique challenges of contractors in a personalized demo.
After the demo you will get a quotation for your company.
After the demo you will get a quotation for your company.