With growing technology, managing construction projects has never been simple. But it wasn’t always like this, and the majority of the industry in the UAE is yet to adapt to this change. Many construction firms find themselves spending valuable time on paperwork and manual processes instead of focusing on delivering value.
Whether it's tracking deliveries, coordinating subcontractors, or keeping documentation current, traditional methods of managing construction projects often leave room for costly mistakes and delays. However, there's now a transformative shift happening in the industry.
The construction workflow automation market, valued at $4.3 billion in 2023, is expanding rapidly with an expected growth rate of 8.5% through 2032.[?]
This growth reflects the industry's recognition that automation and digital solutions can address long-standing operational challenges.
When processes are streamlined and well-organized, projects run smoother, teams collaborate better, and outcomes become more predictable. From initial planning to final handover, each phase benefits from structured workflows that reduce errors, save time, and maintain quality standards.
This article explores how construction workflow automation can help contractors overcome common challenges and position their businesses for sustainable growth in an increasingly competitive market.
What is Construction Workflow?
Construction workflow refers to the systematic sequence of activities, tasks, and processes that take place throughout a construction project's lifecycle. It includes everything from initial planning and design to project completion and handover.
A well-organized workflow ensures materials, labor, equipment, and information move smoothly between different stakeholders and construction phases to deliver successful project outcomes.
Key Components of Construction Workflow Management
For successful workflow management that supports the all five phrases of construction projects, several key components need to work together seamlessly:
- Project planning and scheduling
- Document management
- Resource coordination
- Quality control processes
- Communication channels
- Progress tracking
An effective workflow management system relies on these components to keep teams organized and focused on project goals.
Why is Construction Workflow So Important?
Well-managed construction workflows make projects more profitable in several practical ways:
- Cutting delays by coordinating material deliveries with work schedules
- Reducing waste by planning exact material quantities needed for each phase
- Making better use of resources by scheduling workers and equipment at the right time and place
Building on these efficiency benefits, good workflows also help manage risks through:
- Creating clear timelines for inspections
- Maintaining digital records of all changes
- Enabling quick responses to any site issues
These risk management advantages naturally lead to better team performance. When teams follow structured workflows, they have access to the same up-to-date information, know exactly when their tasks should start and finish, and understand how their work connects with others. This results in fewer errors, faster problem-solving, and better-quality construction.
Ultimately, the impact of proper workflow management extends to the project's bottom line. With tight profit margins and strict deadlines in construction, having effective workflow management often determines whether a project succeeds or fails.
For example, when workflows are properly managed, tasks like concrete pours are scheduled with consideration for weather conditions, crew availability, and equipment readiness, ensuring work gets done right the first time.
5 Signs of Effective Construction Workflow
Before diving into specific indicators, it's important to understand what distinguishes a well-functioning workflow from an average one. These key signs will help you evaluate and improve your current processes.
Sign 1: Clear Communication Channels
A well-functioning workflow features streamlined information exchange between all project participants. You'll recognize this when project updates reach relevant team members without delays, RFIs receive prompt responses, and field teams can access current documentation without repeatedly requesting it from the office.
If your communication system needs improvement, establishing a centralized digital platform serves as the foundation. Daily stand-up meetings between field supervisors and office staff, lasting no more than 15 minutes, create consistent information flow.
Standardized communication protocols — routing structural concerns directly to engineers through project management software, or sharing material delivery updates via designated channels — eliminate confusion and delays. Having a communication coordinator maintain these systems during implementation ensures smooth adoption across the team.
Sign 2: Standardized Documentation
Efficient workflow relies on consistent documentation practices. Your system is working when every team member follows the same templates and naming conventions, documents are easily retrievable, and there's no confusion about where to find or store project information.
For teams struggling with documentation consistency, implementing a structured system starts with creating clear templates and filing protocols. Establish a standardized naming convention for all project documents — for example, "ProjectName_DocumentType_Date_Version."
Develop a document control matrix that specifies review and approval workflows for different document types, from submittals to change orders. Regular training sessions and quick-reference guides help team members adapt to these new protocols.
Sign 3: Predictable Resource Management
In a mature workflow, resource allocation runs like clockwork. You'll notice this when your three-week look-ahead schedules accurately predict labor needs, equipment requirements align with actual usage, and material deliveries arrive just when needed.
To enhance resource predictability, start with detailed activity breakdown structures that specify exact resource requirements. Implement regular weekly resource forecasts that account for project phases, weather conditions, and sequencing dependencies.
Create buffer zones in your schedule for high-risk activities and maintain strong relationships with multiple suppliers to ensure backup options for critical materials.
Sign 4: Measurable Progress Tracking
Effective progress tracking manifests in real-time project visibility. Your tracking system works when you can instantly determine percentage complete for any activity, identify schedule variances, and forecast completion dates with confidence.
Building a robust tracking system begins with establishing clear metrics for each project phase. Integrate digital tools that capture field progress data through mobile devices, allowing real-time updates to project dashboards. Create milestone-based reporting structures that align with payment schedules and owner requirements, ensuring all stakeholders maintain clear visibility into project status.
Sign 5: Integrated Quality Control
Quality management in an effective workflow isn't a separate function but an integral part of daily operations. You'll recognize this when inspection points are clearly defined, quality checks occur naturally within the construction sequence, and defects are caught and addressed early.
Moving toward integrated quality control requires embedding verification points throughout your construction process. Develop activity-specific quality checklists that align with industry standards and project specifications. Institute a pre-task planning process where quality requirements are reviewed before work begins.
Implement digital quality management tools that allow field personnel to document inspections and track issues to resolution, creating a seamless connection between quality control and project progression.
Achieve peak productivity on site
Manage teams, equipment, and materials in FirstBit
Request a demo
5 Construction Workflows to Improve
Construction workflow often suffers from manual processes and disconnected systems, leading to delays, errors, and cost overruns. By implementing digital solutions, you can transform these critical processes into streamlined, efficient operations.
Let's examine the key workflows where automation creates the most significant impact.
1. Cost and Budget Management Workflow
Construction financial management traditionally involves multiple spreadsheets, manual data entry, and delayed reporting. You might recognize these pain points when budget updates take days to process, cost overruns are discovered too late, or when reconciling actual costs with estimates becomes a major monthly challenge.
For companies seeking to streamline their financial processes, solutions like FirstBit ERP offer real-time cost tracking and automated budget management. The system captures all financial transactions instantly, from material purchases to subcontractor payments, providing immediate visibility into project costs.
Budget variations trigger automatic alerts, allowing project managers to address issues before they escalate. The multi-currency support ensures accurate financial tracking for international projects, while automated cost allocation helps maintain precise job costing.
2. Inventory and Material Management Workflow
Traditional material management relies heavily on manual stock counts, paper-based requisitions, and reactive ordering. To improve it and maintain effective resource allocation and inventory well-being, integrate the construction workflow management system in your project.
Basically, you can implement a Warehouse Management System (WMS) to increase inventory performance. However, if you need to improve each part of the chain in your construction project workflow it will work better with ERP.
Let us assure you, some ERP systems for construction include Warehouse Management Module in it. For instance, FirstBit ERP system maintains real-time stock levels across multiple locations. The system helps generate purchase requisitions based on minimum stock levels and project requirements. Material consumption is tracked against specific project codes, providing accurate cost allocation and usage patterns.
3. Purchase Order and Procurement Workflow
Traditional procurement in construction relies heavily on manual processes. Email chains, paper forms, and verbal communications create a complex web of approvals that slows down purchasing. As a result, projects face delayed deliveries, misplaced documentation, and poor visibility into spending.
ERP systems transform procurement by automating the approval process. The system routes purchase requisitions to appropriate approvers based on predefined thresholds and project requirements. With a comprehensive vendor database that tracks performance history and contracted rates, teams can make smarter supplier choices.
The system's integration with inventory management ensures purchases match real project demands. Take a look at how this is implemented in FirstBit:
4. Project Documentation Workflow
If your construction documentation often suffers from version control issues, delayed distributions, and difficult retrieval processes — try to use construction workflow management software. It will centralize all project documentation with automated version control.
Such construction workflow software as FirstBit ERP tracks every document change and approval, creating a complete audit trail. When critical documents are updated, team members receive instant notifications, keeping everyone informed. Field teams can access current drawings and specifications from their mobile devices, ensuring they always work with the latest versions.
5. Payment and Billing Workflow
Slow, manual payment processes create headaches for everyone. When invoices need to be created by hand, routed for physical approvals, and processed with delays, it strains relationships with subcontractors and suppliers while creating cash flow problems.
Construction workflow management systems streamline the payment cycle. Software like FirstBit ERP automatically matches incoming invoices with purchase orders and routes them through approval workflows based on preset criteria. Payment scheduling helps optimize cash flow, while integration with project costing ensures every payment is properly tracked against project budgets.
Trends Shaping Modern Construction Workflows
While established processes remain fundamental, several emerging trends are gaining significant momentum in today's construction industry.
AI in Construction Workflow Management
The integration of Artificial Intelligence (AI) and predictive analytics is transforming how construction workflow processes operate. By analyzing historical project data, these technologies enable smarter decision-making and more accurate forecasting. Project management has evolved with AI-powered tools that process real-time data to identify patterns and potential issues before they impact timelines.
The construction industry is rapidly embracing technological innovation, as evidenced by projects like NEOM in Saudi Arabia and Dubai's initiatives.
For example, NEOM, with its ambitious $500 billion budget, is leveraging AI and robotics to optimize resource utilization and enhance team collaboration.[?]
1. Digital Transformation through BIM
Technological advancements have made Building Information Modeling (BIM) an essential tool in modern construction workflows. This approach creates precise digital models of physical structures, serving as a single source of truth for all project stakeholders. Through BIM integration, teams achieve better coordination and can implement changes efficiently across the entire project lifecycle.
2. Sustainable Construction Workflow
Environmental awareness is driving new approaches to construction workflow management. Today's systems integrate sustainability tracking directly into core processes, making it easier to monitor resource usage and environmental impact. This focus on sustainability helps organizations meet regulatory requirements while maintaining their environmental commitments.
3. Remote Project Oversight
The shift toward remote work has transformed how construction projects are managed. Teams now rely on digital tools to track progress, approve changes, and coordinate tasks from any location. This trend toward remote management continues to grow, making real-time project visibility and collaboration essential for modern construction workflow.
Stay ahead of delays
Monitor project progress with FirstBit
Request a demo
Final Thoughts
As construction projects become increasingly complex, the key to success lies not just in adopting new technologies, but in fostering a culture of continuous improvement. Start by evaluating your current workflows and identifying areas where small changes could lead to significant improvements. Remember that even the most sophisticated systems are only as effective as the teams using them.
Focus on training your staff and building their confidence with new tools gradually. Consider implementing changes in phases rather than attempting a complete overhaul at once. Most importantly, maintain open channels for feedback from your team members who use these systems daily – their insights often lead to the most practical improvements.
Success in modern construction isn't just about having the right tools — it's about creating an environment where efficiency, collaboration, and innovation can thrive. By taking thoughtful steps toward improvement while keeping your team's needs in mind, you'll build not just better projects, but stronger, more capable organizations. If you're looking for a comprehensive solution to streamline your construction workflow, FirstBit ERP can help you transform your operations with proven industry-specific tools and expertise.

Anna Fischer
Construction Content Writer
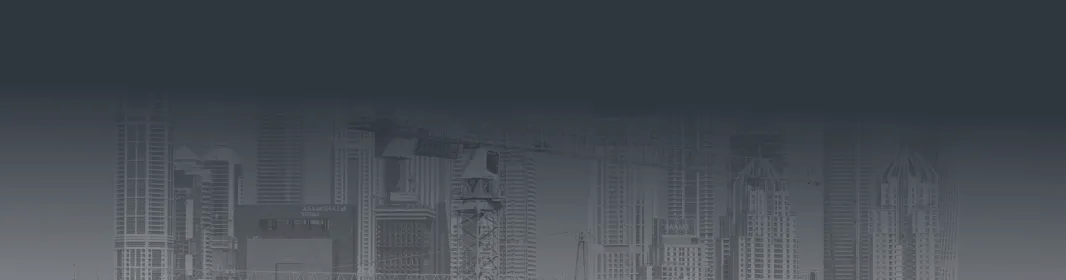
See FirstBit ERP solutions in action
Discover how our system solves the unique challenges of contractors in a personalized demo.
After the demo you will get a quotation for your company.
After the demo you will get a quotation for your company.