In today's fast-paced construction industry, managing equipment effectively can make or break a project's success. With multiple assets spread across different locations, the challenge of tracking equipment usage, availability, and maintenance can quickly escalate, leading to costly delays, lost productivity, and budget overruns.
As a construction professional, you understand that every piece of equipment needs to be in the right place, at the right time, and in top working conditions to ensure seamless operations.
Fortunately, modern equipment tracking systems provide a solution to these challenges by giving construction teams real-time visibility over their assets and enabling better decision-making and resource allocation. This article will explore what equipment tracking in construction is and how to use it to better manage operations.
What is Construction Equipment Tracking
Simply put, construction Equipment tracking helps project managers monitor their equipment. It tells them where the equipment is and how long it is scheduled to be in use. With most systems, you can add scheduled downtime to plan maintenance for certain equipment.
For instance, let’s say the excavator is scheduled for maintenance after 500 hours of operation. The tracking system alerts the project manager when it’s nearing this limit, which lets them schedule downtime for the maintenance without impacting project timelines.
What Type of Equipment Can Be Tracked With an Equipment Tracker?
When it comes to equipment tracking in construction, virtually any type of asset, regardless of size or function, can be monitored and managed. Here are the main categories of equipment that can be tracked:
-
Heavy machinery. These are the backbone of any construction project and include items like excavators, bulldozers, cranes, and loaders. Since these machines are critical to project timelines and often represent a large financial investment, tracking their location, usage, and maintenance is essential for optimizing operations and extending their lifespan.
-
Power tools. Smaller, portable tools such as drills, saws, and grinders are easy to misplace, especially on large sites with multiple crews. Tracking systems help you monitor their whereabouts so they’re always available when needed and reduce the risk of loss or theft.
-
Vehicles. Construction companies often own fleets of vehicles, including trucks, vans, and service vehicles. Tracking these vehicles not only helps manage fuel and maintenance costs but also helps determine the optimal routes they go through.
Tracking your vehicles is not only location-based. Most Equipment tracking systems come with a maintenance tracking system so you can schedule downtime and make sure the vehicles don’t go too long without maintenance.
-
Attachments and accessories. Excavator buckets, blades, augers, and other specialized attachments can often be overlooked during manual inventory checks. By tracking these items, you can ensure they are used appropriately and not left behind at a job site or misplaced.
-
Temporary site infrastructure. Items such as scaffolding, generators, portable lighting, and HVAC units are essential to smooth operations on-site. Tracking these assets helps ensure that critical infrastructure is always available and prevents costly delays associated with missing equipment.
-
Safety equipment. Personal protective equipment (PPE) like helmets, harnesses, and safety gear can also be tracked to ensure that safety standards are maintained and that equipment is replaced as needed. This is particularly useful for large-scale projects where inventory oversight is more difficult.
Key Benefits of Construction Equipment Tracking:
Tracking your construction equipment comes with additional benefits besides knowing where your equipment is.
-
Better management of tools and equipment. With equipment tracking systems, you know exactly what your equipment is being used for and how long it will be in use. This way, you won’t double-book your equipment. This also helps ensure that all tools and machinery are fully utilized and not sitting idle.
-
Managing maintenance and replacements before things break down. Maintaining equipment is cheaper than buying replacements. So, by keeping a maintenance schedule, you’ll be able to prevent unexpected costs.
-
Better resource allocation. With information on resources, you can prioritize resource allocation to urgent tasks and ensure that all projects have enough equipment or tools to finish the project efficiently without delays.
-
Alerts to prevent unplanned downtime and schedule maintenance. Equipment tracking systems often allow you to inset alerts to warn you when maintenance is needed before allocating the equipment to a new project.
-
Minimized loss and theft. Construction sites are notorious for equipment misplaced or stolen. With tracking technology, you can pinpoint the exact location of your assets in real-time and reduce the chances of loss or theft. If equipment is moved off-site unexpectedly, tracking alerts can help recover assets quickly, which helps prevent costly replacements.
Types of Equipment Tracking
The needs of different industries are also different, so there are multiple ways of tracking equipment. The type of tracking will depend on the type of equipment you are trying to track. Some of the most common types of equipment tracking are:
1. GPS tracking
GPS tracking is often used for vehicles and movable equipment such as excavators, cranes, and transport vehicles. When you install a GPS tracker on these types of equipment, you will be able to see a lot of information on its status. For example, you can remotely track the location, see the location history, track the usage of the equipment, and create a maintenance schedule.
2. RFID tracking
An RFID tag might be the best way to implement system tracking for smaller tools. With an active RFID system, the tag will send its own signals, updating the user remotely with new information. To use this, you will need RFID tags, an RFID reader, an antenna, and a computer to collect all the data.
When allocating equipment to a certain project, you can load the RFID tag with information about this project, such as the location, the person responsible for this specific piece of equipment, and the date it was given to the worker.
3. QR-Code or Barcode tracking
Having a tracking system with barcodes or QR codes can be beneficial for keeping track of stock and available resources. Each resource will get its own barcode, and whenever it is used for a project, these will be scanned so the stock will be updated. This way, the project manager can ensure that there is enough material at all times, preventing delays and extra costs.
4. BLE (Bluetooth Low Energy) Tracking
BLE beacons are small, battery-operated devices that transmit signals to nearby Bluetooth-enabled devices like smartphones or tablets. BLE tracking is cost-effective and works well in environments with unreliable GPS signals (e.g., indoor spaces). This type of tracking is often used for indoor equipment, hand tools, or materials stored in warehouses.
5. NFC (Near Field Communication)
NFC tracking is similar to RFID but relies on close proximity scanning. NFC tags are typically used for smaller equipment, tools, or materials that must be monitored when checked in or out. This method is effective for on-site inventory control and can be paired with mobile devices for easy access.
6. IoT (Internet of Things) Tracking
IoT-enabled devices are becoming increasingly popular in construction. Sensors are embedded into equipment, allowing for real-time tracking of not just location, but also performance metrics such as temperature, vibration, and usage patterns. This tracking can give construction companies valuable insights into equipment health, which prevents breakdowns and optimizes efficiency.
7. Telematics
Telematics combines GPS with sensors to provide detailed reports on equipment usage, fuel consumption, idle time, and engine performance. It is commonly used for heavy equipment and vehicles. This allows construction managers to understand better how equipment is being used and identify areas for improvement in operational efficiency.
Systems like FirstBit ERP incorporate several types of equipment tracking to streamline asset management for construction companies. Through FirstBit's system, construction teams can utilize barcodes, QR codes, and RFID tracking to maintain real-time records of their tools, equipment, and materials.
Top Construction Technologies 2024
When it comes to choosing equipment tracking, there are a lot of different solutions and providers who will give you options. However, not all of these solutions will be the right ones for your business. To help you find the option that fits your needs best, we have listed some factors to consider before you choose the right equipment tracking system.
1. Identity Your Requirements
Before implementing a new equipment tracking system, you must know what you want from the system tracker.
-
How do you want to track equipment? Decide if you need real-time tracking (e.g., GPS for vehicles) or periodic updates (e.g., RFID for tools). Determine if geofencing or automatic alerts are necessary.
-
Who needs access? Define access levels based on roles—site managers may need real-time data, while executives may only need reports. Consider data security and external access.
-
What information needs to be tracked? Identify critical data like location, usage hours, and maintenance schedules. Different equipment may require different data points.
-
Integration with existing systems? Make sure the system integrates smoothly with your ERP or project management tools and aligns with your workflows.
-
Budget and scalability? Define your budget for initial setup and ongoing costs, and ensure the system can grow with your company.
Additional questions:
-
What equipment types are tracked?
-
Do you need mobile access?
-
Should the system provide automated maintenance alerts?
-
How will you measure the system’s success?
Once you have listed your requirements, you’ll be able to narrow down your options further to the ones that meet these unique needs. Then, you can assess the remaining options based on the rest of the criteria below.
2. Key Features to Look For
All best equipment tracking systems will have the following features:
-
Real-time tracking: Provides live updates on the location of vehicles, tools, and machinery, ensuring you always know where your assets are.
-
Usage monitoring: Tracks equipment usage hours, idle time, and performance, allowing you to optimize asset utilization and prevent overuse.
-
Maintenance alerts: Automatically schedules and notifies you of upcoming maintenance based on usage, reducing downtime and preventing equipment breakdowns.
-
Geofencing: Sends alerts when equipment moves in or out of predefined areas, preventing unauthorized usage or theft.
-
Inventory management: Keeps a detailed inventory of all assets, including availability, location, and condition, ensuring efficient allocation across projects.
-
Mobile access: Enables field staff to track and manage equipment via smartphones or tablets, offering flexibility on the go.
-
Reporting & analytics: Generates reports on equipment usage, maintenance, and overall performance, helping you make data-driven decisions.
-
Integration capabilities: Seamlessly integrates with your existing ERP, project management, or accounting software for streamlined operations.
-
User permissions: Allows role-based access, ensuring that the right team members have access to the necessary data while maintaining security.
-
Scalability: Adapts to the growth of your business, easily accommodating additional assets, users, and projects as needed.
3. Evaluate User-Friendliness
Evaluating how easy an equipment tracking system is to use is important because it directly affects how well you can manage your tools and machinery. The entire idea behind it is to make your work easier. If the system is hard to understand or overly complicated, it can lead to mistakes and waste your time.
A good system should be simple to navigate and let you easily view all your current equipment in one place. It should also be straightforward to add new tools or equipment without any hassle.
Clear instructions, intuitive design, and easy access to information are essential features that ensure the system will support your work rather than slow it down.
4. Assess Cost vs. Value
Within construction, there is always a tight budget, so when you are looking to implement an equipment tracking system, the price of the system is something to keep in mind. Assess the cost of the system versus the value it will bring to your business.
For example, the initial investment to implement equipment tracking systems is often worth it if you have tools and machinery scheduled to be used in different projects. If you have a large inventory and need to keep track of your available resources to prevent the costs that come with delays, a tracking system can keep costs within your budget.
With most tracking services, you must pay a monthly fee to maintain the systems. This is an additional cost that must be considered when making budgets.
Check for Compatibility
Not all equipment tracking services will work with your style of work. So, checking if your equipment is compatible with the tracking systems is important to avoid wasting money on something that does not work for you.
Some tracking systems require you to upgrade computers or other tools to be able to work with the software or technology from the trackers. This would add to the cost of the tracker and is not always worth it.
The companies providing the system tracking solutions often have a list of all the required technology or needed equipment, to be able to use their services. If they don’t, you can always contact them for more information to make sure their services work with your current setup.
5. Read Reviews and Get References
Reading reviews from people in the same industry who have used the equipment before is a great way to gain insight into the tracking systems you are considering. The reviews can give you key information on things you wouldn’t be able to tell without actually using the product, such as:
-
User-friendliness
-
Longevity of the trackers
-
Reliability of the services
No company will promote its flaws when trying to sell you something, so the reviews from real people will give you a different perspective on the service you’re looking into.
Companies that stand true to their claims often share detailed case studies from their clients to help you see the success their systems brought to these clients. For example, FirstBit has a dedicated blog where you can see detailed case studies, expert reviews, and client testimonials, along with their contact information, for increased transparency.
6. Request a Demo or Trial
Before making the final decision, ask for a trial period or a demo to prove that the service and the tracking system will fit your company. After the demo or trial, you can decide whether to continue with the service or choose another option.
Each of these demos or trial periods is unique to the company offering them. Some will provide you with a limited-time trial with full access to their systems' capabilities. Others will give you access to basic functionalities for a more extended period.
Streamlining Equipment Tracking with First Bit ERP:
The FirstBit tracking system software gives you access to a whole lot of information on equipment and resources. Some of the features you can expect from the software are:
-
Resource allocation to plan the full project efficiently. This way, you make sure you have the right equipment and materials at the start of a project.
-
Double Booking prevention, to prevent tools or resources from being allocated to different projects at the same time.
-
Transfer history, which is important to keep track of people who have used the tools and where the tools have been transferred to.
-
A database of information: FirstBit ERP has a database with information on the status of the equipment, its location, who is responsible for it, and how to transfer it to someone else.
With these features, you can efficiently manage your construction projects without having to worry about equipment, resources, or maintenance. This will also make staying within budget a lot easier.
FAQs
1. How does equipment tracking help reduce costs in UAE construction projects?
2. Is equipment tracking mandatory in the UAE construction industry?
3. Can equipment tracking systems integrate with construction ERP software in the UAE?
4. What is the cost-benefit of implementing an equipment tracking system in UAE construction projects?

Imanu Baldussu
Contributing Author
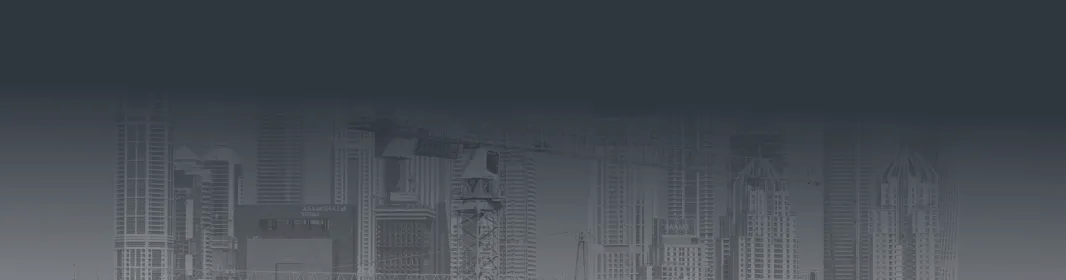
See FirstBit ERP solutions in action
Discover how our system solves the unique challenges of contractors in a personalized demo.
After the demo you will get a quotation for your company.
After the demo you will get a quotation for your company.