For many new construction business owners, the journey from project inception to completion can feel like navigating a maze of shifting timelines, budgets, and expectations. The pressure to deliver quality work on time and within budget often brings with it a range of challenges.
One misstep in planning or execution can ripple through the entire project, leading to delays, cost overruns, or even strained client relationships. That’s why understanding the five key phases of a construction project is crucial.
This guide breaks down each phase, providing you with a roadmap to ensure every stage of your project runs smoothly. Following these closely will help you avoid common pitfalls and meet client expectations.
What are the 5 Stages of a Construction Project?
A well-structured construction project typically unfolds across five distinct project phases.
Phase 1: Project Initiation
This is where the project's foundation is laid — defining the scope, setting goals, assembling your team, and securing initial funding.
Steps in Project Initiation
-
Project conception. Transform the initial idea into a concrete plan by outlining key needs and objectives.
-
Feasibility study. Conduct an in-depth analysis of the project's viability by assessing risks, evaluating budget feasibility, and reviewing regulatory requirements.
-
Project scope development. Clearly define the project's boundaries, deliverables, and key performance indicators (KPIs).
-
Team formation. Assemble a skilled project team of architects, engineers, contractors, and other essential personnel.
-
Securing initial funding. Secure the necessary financial resources to advance through the initial project stages.
Challenges
-
Idea refinement. The challenge lies in differing visions and goals among stakeholders. Stakeholders may struggle to agree on key objectives and priorities.
-
Viability assessment. Accurately evaluating project feasibility involves complex analysis. Unforeseen risks or regulatory issues can derail the project early on.
-
Scope definition. Setting clear project boundaries and deliverables is often challenging. Stakeholders may have conflicting views on what should be included or excluded.
-
Team assembly. Finding the right mix of skilled professionals can be difficult. Coordinating schedules and managing diverse expertise adds complexity.
-
Funding challenges. Securing initial financial resources can be a major hurdle. Convincing investors or lenders of the project's value may require extensive effort.
How to Optimize the Project Initiation Phase
-
Conduct thorough research and risk assessments early, and consult with experts to ensure all aspects are addressed.
-
Invest time in thorough planning to create a solid foundation. Solid planning starts with clearly defining the project's goals, objectives, and scope. Break down the project into smaller, manageable phases or milestones. Identify potential risks and develop mitigation strategies early on. A well-defined project charter or scope statement acts as a roadmap and keeps the project focused.
-
Ensure all stakeholders (client, team, investors) have a shared understanding and agreement from the project's beginning. Hold kickoff meetings and workshops to bring all stakeholders together. Clearly communicate project goals, timelines, and individual responsibilities. Document decisions and agreements in a shared location accessible to everyone. Regularly communicate progress updates and address any emerging concerns promptly. This fosters collaboration and prevents misunderstandings down the line.
-
Conduct a detailed cost analysis with contingency planning. A detailed cost analysis involves identifying all potential costs, including direct costs (materials, labor) and indirect costs (administration, overheads). Research market rates for resources and obtain quotes from vendors. Develop a realistic budget that reflects the project scope. Crucially, incorporate a contingency buffer (e.g., 5-10% of the total budget) for unexpected expenses or delays. For instance, if your estimated project cost is $100,000, set aside $5,000-$10,000 for contingencies. This buffer can cover unforeseen issues like material price increases or minor design changes.
-
Use special software such as ERP system for activities planning and bill of quantities (BOQ) estimating. Leverage project management software or ERP systems to streamline planning, scheduling, and resource allocation. These tools can automate tasks, track progress, and generate accurate bills of quantities (BOQ). A BOQ provides a detailed breakdown of materials, labor, and costs required for each project component, ensuring accurate cost estimation and efficient resource management. Choosing the right software can significantly improve project efficiency and accuracy.
Phase 2: Pre-Construction
With the project blueprint established, the pre-construction phase focuses on thorough planning and preparation.
Steps in Pre-Construction
-
Design development. Architects and engineers must translate the conceptual design into detailed construction drawings and specifications.
-
Permitting and approvals. Secure all necessary permits and approvals from local authorities.
-
Contractor selection. Conduct a rigorous bidding process to select the most qualified contractors and subcontractors.
-
Budget finalization. Develop a budget based on detailed designs and contractor bids. Start by gathering detailed designs and specifications. Then, request bids from multiple contractors based on these specifications. Compare the bids carefully, noting any discrepancies. Use the most competitive bids to create your budget, including a contingency for unforeseen expenses.
-
Scheduling. For realistic project scheduling, break down the project into smaller, manageable tasks for accurate time estimation. Consult with team members on individual task durations and incorporate buffer time for unexpected delays. Regularly review and adjust the schedule as needed to stay on track.
Challenges
-
Design complexity. Turning concepts into detailed plans can be challenging. Architects and engineers may struggle to align all aspects of the design.
-
Permit hurdles. Obtaining necessary approvals can be time-consuming and unpredictable. Local authorities may require multiple revisions or additional documentation.
-
Contractor dilemmas. Selecting the right contractors is crucial but difficult. Comparing bids and qualifications can be complex and time-intensive.
-
Budget uncertainty. Accurately estimating costs based on designs and bids is tricky. Unforeseen expenses can quickly derail even well-planned budgets.
-
Schedule conflicts. Creating a realistic timeline for complex projects is challenging. Unexpected delays can easily throw off carefully planned schedules.
How to Optimize the Pre-Construction Phase
-
Use collaborative design software like BIM to ensure everyone is on the same page. Regular team meetings can also help align different aspects of the design.
-
Start the permit process early and maintain regular communication with local authorities. Hiring a consultant who understands local regulations can also ease the process.
-
Develop a list of criteria to evaluate contractors based on past performance and reliability. Use a prequalification process to narrow down the choices quickly.
-
Include a contingency fund for unexpected costs and update the budget regularly. Use historical data to make more accurate cost estimates.
-
Utilize project management tools to outline the timeline and identify task dependencies. Include buffer time for unforeseen delays to keep the project on track. For example, FirstBit ERP system has a project management module that will simplify your workflow.
Phase 3: Procurement
This phase focuses on acquiring the essential materials, equipment, and labor needed for the project.
Steps in Procurement
-
Vendor identification. Establish a reliable network of vendors for materials, equipment, and services. Start by conducting thorough market research to identify potential suppliers that align with your needs and quality standards. Attend industry trade shows, join professional associations, and utilize online platforms to expand your network and discover new vendors.
-
Contract negotiation. Secure favorable terms and conditions with selected vendors. Negotiate based on volume commitments, prompt payment history, and potential for future business growth. Be prepared to offer something in return, such as longer contracts or exclusivity agreements, to incentivize better terms. For example, a construction company might negotiate with a lumber supplier for a 5% discount on all orders by committing to a minimum annual purchase volume and agreeing to pay invoices within 15 days instead of the standard 30 days.
-
Order placement. Place orders for materials and schedule deliveries.
-
Inventory management. Establish systems for tracking, storing, and managing materials efficiently. For example, ERP systems like FirstBit can integrate procurement, storage, and usage data, enabling automated reordering and generating detailed reports for informed decision-making.
Challenges
-
Unreliable suppliers. Finding trustworthy vendors can be time-consuming and challenging. Some suppliers may not meet quality standards or have inconsistent service.
-
Tough negotiations. Securing favorable terms can be difficult, especially for new or small businesses. Vendors may be reluctant to offer discounts or flexible payment terms.
-
Delivery delays. Orders may not arrive on time, disrupting project schedules. Miscommunication about delivery dates or unexpected shipping issues can cause problems.
-
Inventory disorganization. Keeping track of materials and preventing overstocking or shortages can be complex. Manual inventory systems are prone to errors and inefficiencies.
How to Optimize the Procurement Phase
-
Start the procurement process early to secure better pricing and mitigate delays. For instance, by ordering construction materials six months in advance, a builder can lock in lower prices before seasonal demand increases. This early procurement also ensures materials are on-site when needed.
-
Engage with multiple vendors to create competition among them, compel them to give you the best price, and ensure supply chain stability.
-
Implement efficient inventory management techniques like economic order quantity (EOQ), batch tracking, etc., or software to minimize waste and delays or integrate ERP system with inventory management module in it. This module maintains optimal inventory levels and meets customer demand without overstocking. This approach minimizes waste, reduces costs, and ensures product availability.
Phase 4: Construction
This is where the vision transforms into reality. The construction phase involves the physical execution of the project, with contractors and subcontractors working diligently to build according to the established designs and specifications.
Steps in Construction
-
Site preparation. Preparing the construction site, including clearing, grading, and setting up temporary infrastructure.
-
Foundation and framing. Building the foundation and structural framework of the project.
-
MEP installation. Installing essential mechanical, electrical, and plumbing systems.
-
Interior and exterior finishes. Completing interior and exterior finishes, including drywall, painting, flooring, and landscaping.
Challenges
-
Site preparation problems. Bad weather can cause significant delays in outdoor work. Unexpected ground conditions may complicate excavation and site leveling.
-
Foundation and framing. Mistakes in foundation and framing can lead to costly structural issues. Inexperienced workers might make critical errors in measurements or construction techniques.
-
MEP installation issues. Different mechanical, electrical, and plumbing systems may interfere with each other in limited spaces. Improper planning can result in rework and project delays.
-
Interior and exterior finishes. Last-minute design changes can disrupt timelines and material availability. Late decisions on finishes may lead to rushed work and quality issues.
How to Optimize the Construction Phase
-
Monitor weather forecasts and adjust schedules to work around bad weather. Conduct thorough site investigations to anticipate and plan for varying ground conditions.
-
Conduct comprehensive site surveys to identify potential issues upfront. Site surveys should assess topography, soil conditions, existing structures, and potential environmental hazards. They should also evaluate access routes, utility connections, and any local regulations that might impact construction.
-
Coordinate design plans for MEP systems to minimize interference. Use 3D modeling tools to visualize and plan for space constraints.
-
Look for project managers with a proven track record of successful construction projects and relevant certifications like Project Management Professional (PMP) or Certified Construction Manager (CCM). Conduct thorough interviews focusing on their problem-solving skills, communication abilities, and experience with similar project scopes and scales.
-
Prioritize safety protocols and training to minimize accidents and ensure worker well-being. UAE law mandates the use of fall protection systems for work at heights and proper scaffolding with regular inspections. Employers must provide comprehensive safety training, ensure proper use of personal protective equipment (PPE), and maintain a safe working environment with adequate ventilation and emergency response plans.
Phase 5: Post Construction
You've now completed your construction project and it looks great! But hold on, there's still some important work to do before your journey is over. The construction project's path continues even after the physical structure reaches completion. The post-construction phase aims to finalize the project by conducting final inspections and resolving any remaining issues.
Steps in Post-Construction
-
Punch list completion. Conduct a thorough review to uncover and address any defects or unfinished tasks. To do a full review, use a checklist or special software to go through every part of the building project carefully. Look closely at each area, write down any problems or unfinished work, and fix them right away. While tools like ERP can help keep track of things, the most important part is checking everything in person to make sure it's all done right.
-
Final inspections. Schedule and pass final inspections by local authorities. For example, if you built an office building, have the city's building department, fire department, and electrical inspector conduct their final checks to make sure everything is safe and up to code. These inspections will look at things like the building's structure, fire safety systems, and electrical wiring to ensure the building is ready for people to use.
-
Documentation and closeout. Finalize all project documentation, including as-built drawings, warranties, and operation manuals. This will help businesses keep track of what was built and how to take care of it. It also makes sure they have all the information they need if something breaks or needs fixing in the future.
-
Project handover. Officially transfer ownership and responsibility of the project to the client. When transferring ownership, make sure all legal documents are properly signed and filed. Be careful to clearly explain any ongoing maintenance needs or warranty conditions to the client to avoid future misunderstandings.
Challenges
-
Overlooking defects. Small issues might be missed during review. Multiple team members may have conflicting schedules for thorough checks.
-
Failing inspections. Last-minute issues may arise, leaving little time for fixes before official inspections.
-
Missing documents. Project files can be scattered across different team members. Tracking and organizing all necessary documentation throughout the project also can be overwhelming.
-
Unclear handover. Clients may not fully understand technical aspects of the project. There might be miscommunication about ongoing maintenance needs or warranty conditions.
How to Optimize the Post-Construction Phase
-
Plan an early internal inspection to identify potential problems. Keep a buffer period before the official inspection for necessary fixes.
-
Use a special system, like ERP software, to keep all project files easy to find and use later.
-
Check in with the client regularly after handover to fix any new problems and learn how to do better on future projects.
Tips for the Success of a Construction Project
While each phase presents unique challenges, several overarching tips can contribute significantly to a successful construction project.
1. Create a Detailed Plan
Ensure the success of your construction project with a well-defined plan. Use this blueprint to guide every step from start to finish. Clearly specify project objectives, detailing what needs to be achieved and how. Establish essential timelines, breaking the project into manageable phases with realistic deadlines.
Assign clear responsibilities and make sure everyone understands their role and reporting structure. This careful planning minimizes confusion and keeps the project progressing smoothly.
2. Monitor the Progress of the Project
Oversee the project regularly to spot deviations from the initial plan and act quickly to correct them. Compare actual work with the schedule, analyze resource allocation, and assess team effectiveness.
Consistent monitoring keeps the momentum going, lets you anticipate potential roadblocks, and ensures the project stays on track with the budget and timeline.
3. Ensure Clear Communication
To keep everyone aligned with project goals and prevent misunderstandings, actively maintain open dialogue. Schedule regular meetings, provide progress reports, and set up easy channels for team members to ask questions or raise concerns.
Foster clear communication to identify and resolve issues quickly. This proactive approach leads to a more efficient and harmonious project environment.
4. Strive to Graduate Early
Aim to complete tasks ahead of schedule to enjoy several benefits. This proactive approach creates a time buffer, helping you manage unexpected issues like weather delays, material shortages, or unforeseen site conditions more effectively.
With extra time, you gain the flexibility to resolve problems without interrupting the entire project schedule, which greatly increases the likelihood of finishing the project on time.
5. Prioritize Security
Integrate safety into all aspects of your work to make safety your top priority on the construction site. Begin by conducting regular risk assessments to identify and address hazards quickly. Ensure that all team members receive comprehensive safety training so they understand protocols and emergency procedures.
Enforce the proper use of safety equipment by inspecting gear regularly and making its correct use mandatory at all times. Also, establish a dedicated safety compliance team to monitor adherence to safety measures and empower them to take immediate action when necessary.
Finally, a safety culture should be cultivated by encouraging workers to report any safety concerns or near-misses, using their feedback to improve safety protocols continuously.
Stay ahead of schedule
Control project timelines through FirstBit
Request a demo
How FirstBit ERP Can Streamline the Construction Process
Juggling multiple spreadsheets, managing revisions across different teams, and chasing down approvals can make construction projects feel chaotic. Important information gets siloed, making real-time decision-making nearly impossible and leading to costly delays and budget overruns.
FirstBit ERP streamlines the entire construction process, offering a single source for all project information.
It consolidates all project data into a single, centralized system, eliminating information silos and boosting collaboration. With real-time access to project plans, budgets, and progress reports, everyone stays informed and aligned.
Automated workflows streamline approvals, procurement, and other key processes, reducing manual errors and saving valuable time.
Plus, FirstBit's robust reporting and analytics dashboards provide valuable insights into project performance, empowering data-driven decision-making to optimize resource allocation, manage costs, and ensure on-time project delivery.
With FirstBit ERP, turn your construction challenges into opportunities for excellence. Take the next step toward seamless project management and explore how FirstBit ERP can transform your construction processes today.

Anna Fischer
Construction Content Writer
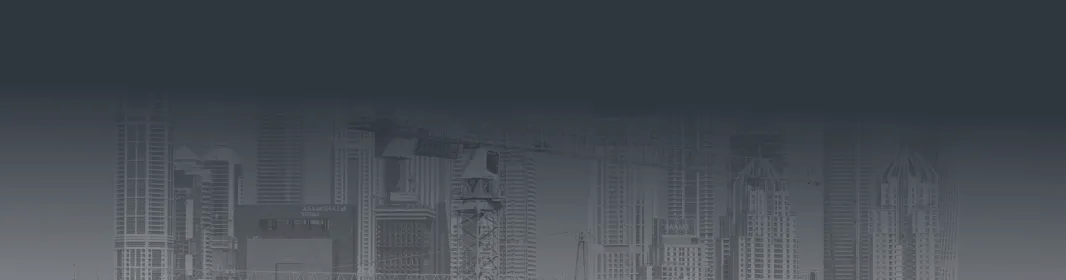
See FirstBit ERP solutions in action
Discover how our system solves the unique challenges of contractors in a personalized demo.
After the demo you will get a quotation for your company.
After the demo you will get a quotation for your company.